Many companies are adopting AI, ML, IoT, Big Data, robotics and other advanced technologies as part of their Industry 4.0 strategy. Now, Industry 5.0 has emerged, shifting focus from automation to human-machine collaboration, empowering workers instead of replacing them. Adopting the new paradigm is crucial for enterprises in manufacturing and other sectors to remain competitive, meet evolving customer expectations, and foster technological advancement. However, this transition also introduces new technological challenges, which companies can address by building the necessary expertise in-house, working with external consultants or partnering with tech vendors that offer advanced manufacturing software development services and have deep expertise in latest tech.
What is Industry 5.0? What is the difference between Industry 4.0 vs 5.0 and how to make this transition? What are the real-life applications of this shift? Discover the answers to these questions and get ready for Industry 5.0 with N-iX.
What is Industry 5.0?
Industry 4.0 presumes the integration of AI/ML, IoT, 3D printing, advanced robotics, and other technologies into manufacturing processes to create interconnected factories that enhance efficiency, productivity, and automation. This automation-centric approach fueled concerns about human workers being replaced by robots.
Recognizing this potential pitfall, the concept of Society 5.0 emerged. This approach aims to create a "super-smart society" that balances economic and technological growth with resolving societal issues and improving quality of life.
Industry 5.0 took inspiration from both Industry 4.0 and Society 5.0, aiming to blend the former's technological advancements with the latter's human-centric focus. The three pillars central to the Industry 5.0 definition are sustainability, human-centricity, and resilience. Unlike its predecessor, this approach focuses on reskilling or upskilling humans rather than replacing them. Therefore, it signifies a transformation in industrial strategy, aiming to integrate advanced technologies with human capabilities and needs.
Learn more about digital transformation in manufacturing
Industry 4.0 vs 5.0 comparison and adoption guidelines
If you have already adopted Industry 4.0, you have a strong foundation to build on. While continuous improvement is essential, the primary focus has shifted. Now, it is time to leverage those advancements to synergize technology and society, ensuring favorable outcomes for all stakeholders.
Efficiency vs human well-being
Industry 4.0 focuses on achieving efficiency, automation, and cost reduction by creating interconnected, smart factories where machines and systems communicate seamlessly to optimize production processes. To progress towards Industry 5.0, shift your focus to integrating advanced technologies with human capabilities to create adaptable, eco-friendly workplaces that prioritize human well-being. You can begin by assessing your current automation systems and identifying opportunities to integrate more human-centric solutions.
Technology utilization
Industry 4.0 leverages technologies for real-time data exchange and extensive automation to improve productive capacity.
- IoT connects machines and devices, facilitating more intelligent decision-making through real-time monitoring.
- AI powers intelligent systems for predictive maintenance and quality control.
- Robotics enhances precision and consistency in manufacturing tasks.
- Big Data analytics help optimize operations, while cloud computing offers scalable data storage and processing resources.
- 3D scanning and printing enable rapid prototyping and highly customizable manufacturing.
To make a transition, build on these technologies and add advanced systems to create more personalized, adaptive solutions. Start by evaluating your current technology stack and identifying gaps where human-machine collaboration can be improved. Here are the possible advancements:
- Advanced AI supports more intuitive interactions and adaptive production processes.
- Cobots work alongside humans, combining human creativity with robotic precision.
- AR provides real-time visual information for guided assembly and maintenance.
- 3D scanning and printing continue to play a crucial role, further integrated with advanced AI to enable more sophisticated, personalized manufacturing solutions.
- Sophisticated human-machine interfaces (HMIs) enhance accessibility and usability through intuitive controls and interactions.
- Exoskeletons reduce physical strain and fatigue of the employees, leading to both increased productivity and preventing injuries.
Learn more about Artificial Intelligence in manufacturing
Automation vs collaboration
In Industry 4.0, the focus is on automation and the digitalization of processes. Machines operate with minimal human intervention, supervised through interconnected systems and real-time data analytics. To make a shift towards the new approach, companies need to enhance joint human-machine operations through advanced technologies like cobots and AR. This change will leverage human creativity and problem-solving abilities. Achieving this goal requires training your workforce to work alongside these technologies and redesigning workflows to incorporate collaborative processes.
Personalization focus
Industry 4.0 achieves personalization through segmentation and mass customization, tailoring products or services to specific customer segments while maintaining mass production. To elevate this in Industry 5.0, aim for hyper-personalization.
Developing products and services that meet the precise demands of individual customers using advanced data analytics, AI, and digital manufacturing technologies is only part of the process. What may be more important is using technologies for personalized manufacturing and worker-centric solutions.
Examples of those solutions include workstations, tools, and protective gear tailored to each worker’s physical dimensions and work habits. Furthermore, wearable technologies and health monitoring systems can be customized to track individual health metrics such as heart rate, posture, and movement patterns. These devices alert workers about potential health issues before they become serious and the data collected is used to develop personalized wellness programs.
Data utilization
Industry 4.0 utilizes data primarily for decision-making and process optimization. Key aspects include:
- Real-time data collection
- Big Data Analytics
- Cloud computing
- Predictive maintenance
- Supply chain optimization
The Industry 5.0 definition presumes to build on Industry 4.0 and utilize data not only for optimizing processes but also for creating more personalized, adaptive, and collaborative solutions that integrate human elements into the manufacturing process. Here are a few examples of how to leverage data to achieve more:
- Enhanced human-machine interaction: Data is used to create more intuitive and adaptive interfaces, improving human-machine collaboration.
- Personalized solutions: Leveraging data to provide customized experiences and solutions tailored to individual needs and preferences.
- Sustainability and resilience: Sustainable practices and resilient systems can help to adapt to changing conditions even in real-time.
- Advanced AI and ML: For adaptive, autonomous systems that improve over time.
Here’s how to make the most of Big Data in manufacturing
Workforce impact
The impact on the workforce varies significantly between the two phases. Industry 4.0 often leads to workforce reduction due to extensive automation. The focus is on minimizing human intervention and relying on smart systems, shifting humans' roles from direct involvement in routine tasks to supervisory roles where they oversee, manage, and optimize the performance of these intelligent systems.
Conversely, Industry 5.0 aims to augment and enhance the workforce. It promotes collaboration between humans and machines, ensuring that technology complements human skills and creativity, leading to a more empowered and skilled workforce. Such an approach results in increased employee motivation and improved retention as it creates opportunities for continuous learning and skill development.
Application examples
The focus on automation and interconnectedness of Industry 4.0 results in applications such as smart factories, which optimize production through interconnected systems; predictive maintenance to prevent equipment failures; automated production lines that minimize human intervention; and supply chain optimization for streamlined logistics and inventory management.
Industry 5.0 shifts towards more personalized and sustainable approaches. It emphasizes custom manufacturing tailored to individual needs, sustainable practices to reduce environmental impact, the integration of human craftsmanship with advanced technologies, and the development of smart cities and infrastructure that enhance urban living through intelligent systems and data-driven management.
Industry 5.0 success stories
A prime example of Industry 5.0 principles in action comes from Audi's implementation of exoskeletons on their assembly lines. These wearable support structures assist workers with physically demanding overhead tasks, reducing muscle fatigue in the thighs, hips, and back. This technology is adaptable, allowing adjustments based on worker height for optimal support. These exoskeletons showcase how Audi prioritizes employees' well-being and empowers them with technology.
Another example of 5.0 in action is Siemens GWE, a German electronics plant. Facing challenges like labor shortages and cost pressures, GWE integrated cobots into its production lines. Unlike most other robots, cobots do not replace human workers but augment them instead. Currently, more than 70 units help GWE’s employees with repetitive or physically demanding tasks. The company plans to implement more robots and leverages digital twins to plan better and minimize disruption. The impact of cobots at GWE extends beyond just increased productivity and cost savings because they allow workers to focus on more engaging activities and make a more motivated workforce.
Read more about applying robotics in manufacturing
Boost efficiency and cut costs in manufacturing with IoT solutions – explore now!
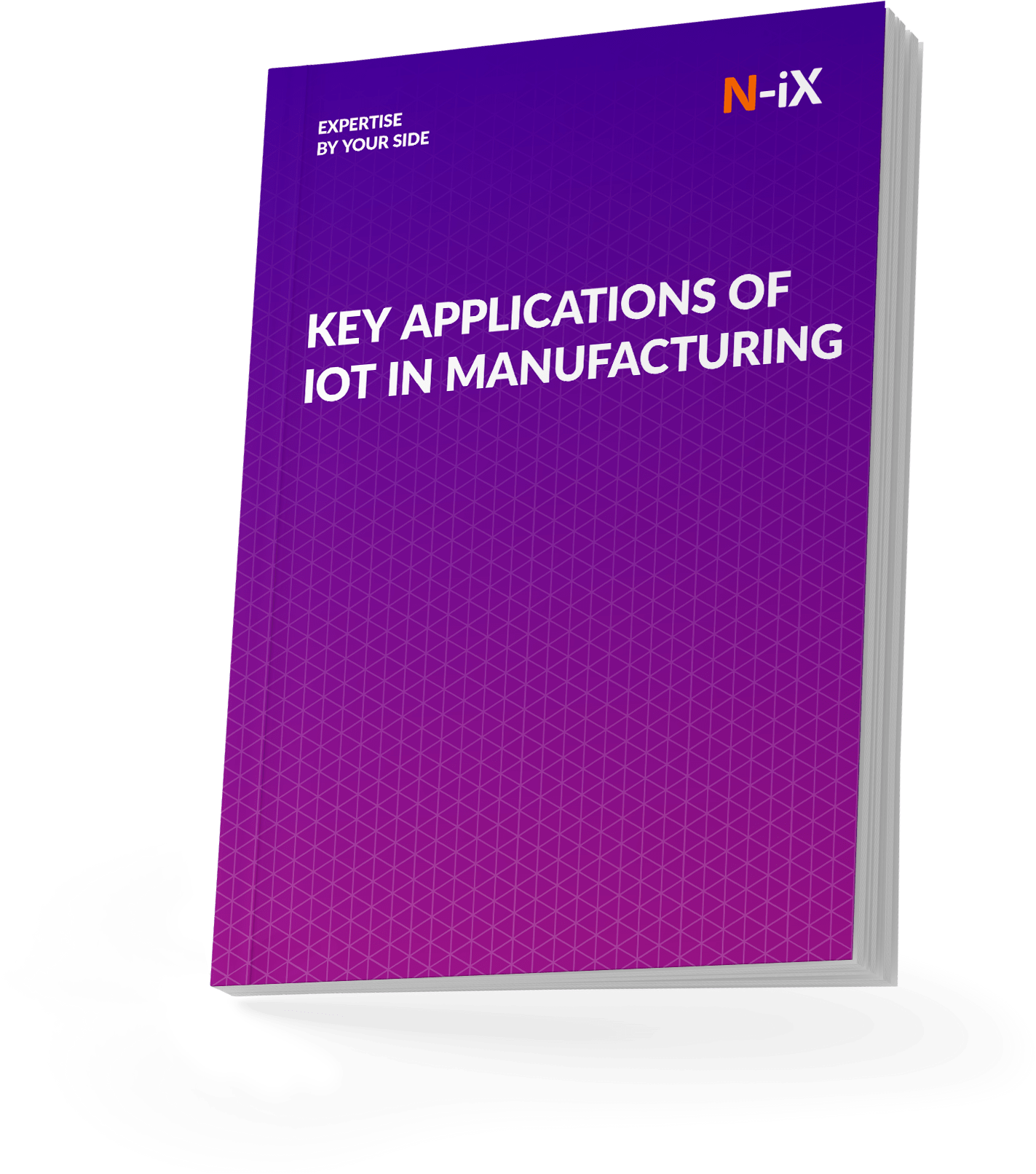
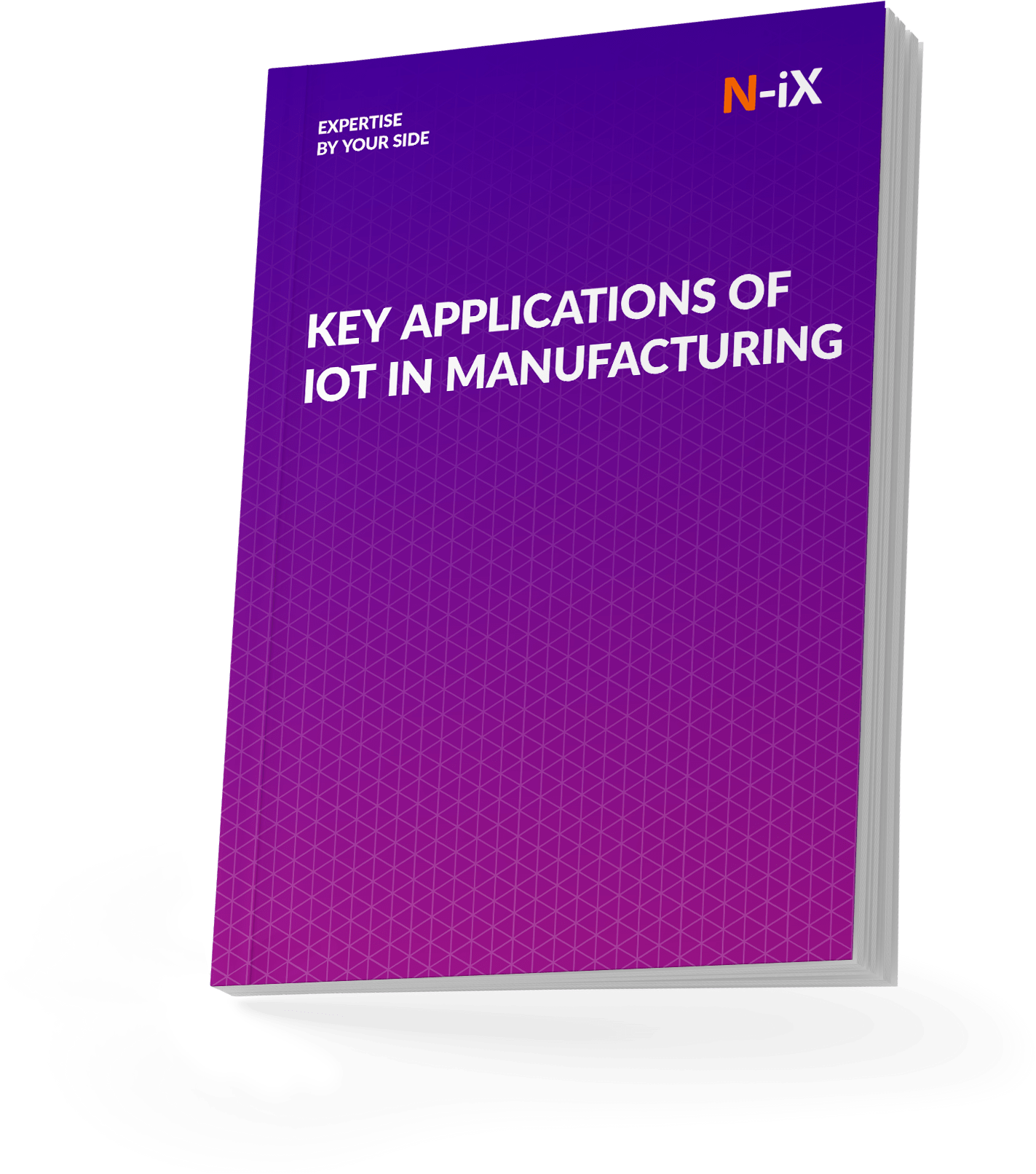
Success!
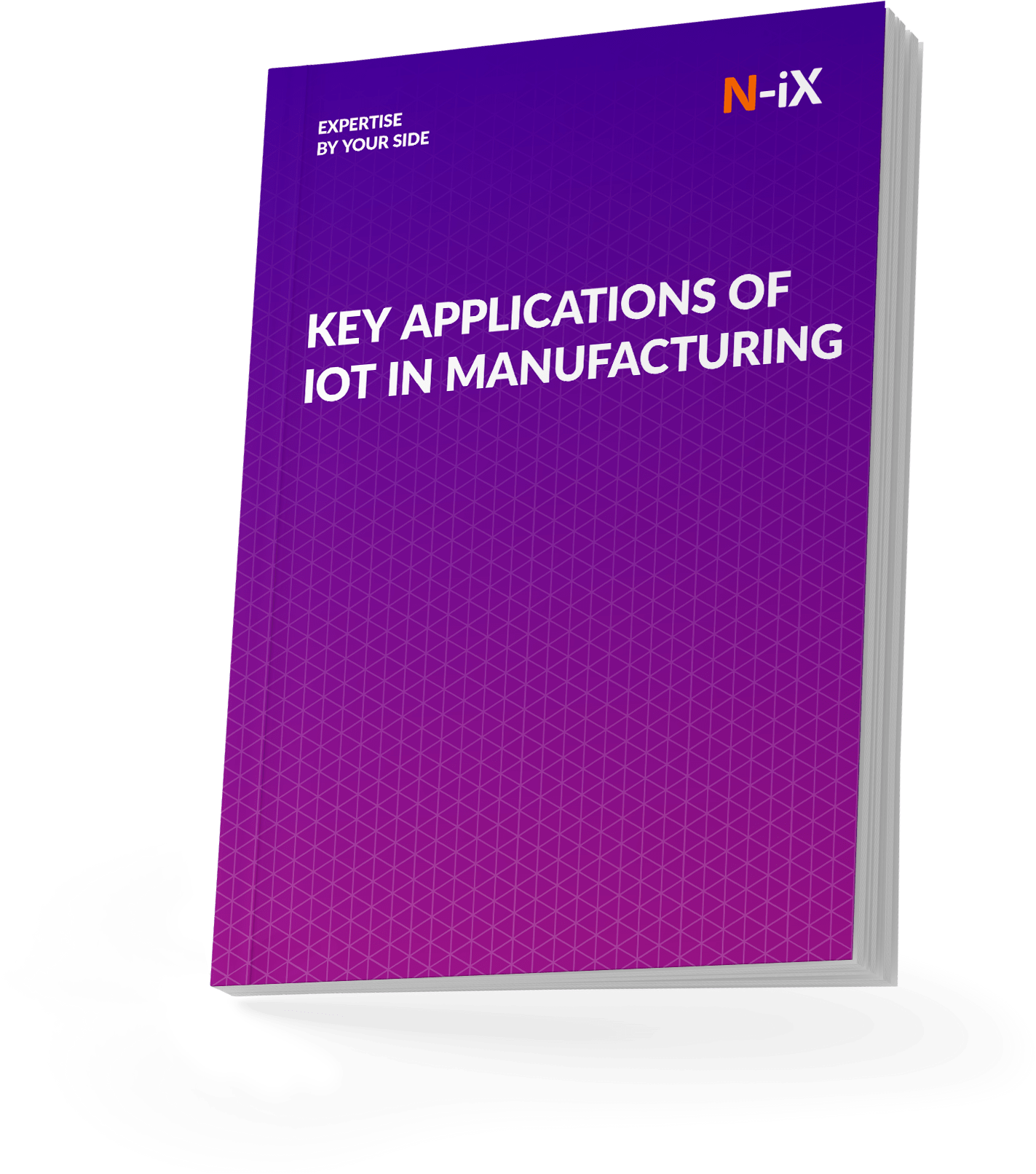
Prepare for Industry 5.0 with N-iX
Manufacturing and related sectors are undergoing a significant shift, building upon the foundations of automation. This period is crucial, as it allows businesses to shape the future by blending efficiency with an approach that aims at human-machine collaboration, resilience, and sustainability.
At N-iX, we commit to driving this transformation forward, ensuring that our clients not only improve their operational efficiency but also develop more inclusive, adaptive, and convenient solutions. With over 200 experts in data, N-iX implements advanced AI/ML solutions that enhance decision-making and personalize user experiences. Our 400 cloud engineers and 60 DevOps experts work collaboratively to create scalable, reliable, and flexible cloud infrastructures. Through our commitment to Industry 5.0 principles, we help clients navigate this transitional period, shaping a future where technology serves humanity.