Sensors are integral in any technical device management system. They find applications in everything from robotic manipulators and automobiles to smartphones. A single sensor provides valuable information and can be utilized in software applications with a certain degree of accuracy. However, their physical nature often makes them insensitive to environmental factors So, they always have an inherent margin of error, potentially limiting their applicability. Thus, industries like automotive and manufacturing have been trying to find a way to adopt various sensors and orchestrate their performance for enhanced results. That’s how the idea of Sensor Fusion emerged on the tech horizons.
What is Sensor Fusion?
Sensor Fusion is a technique that enhances the accuracy of environmental information. The image below illustrates a closed-loop system equipped with a group of sensors and data mixers, along with actuators acting upon the environment.
Common application of Sensor Fusion
Common Sensor Fusion applications include using data from Radar, LiDAR, and cameras to estimate the 3D position of objects surrounding a vehicle. This is achieved by combining data from these sources to enhance the accuracy of object positioning in space. Another example involves using accelerometers, potentiometers, and encoders to precisely determine a vehicle's dynamics. Each sensor has its strengths in sensing physical processes occurring during vehicle acceleration, and their combination offers the most accurate depiction of the scene.
Benefits of Sensor Fusion
1. Enhanced system resilience
Models and sensors are subject to tolerance errors. So, when multiple sensors measure the same parameter, reliability and resilience can be enhanced. Even though redundancy adds complexity and cost, overlooking it can result in catastrophic single points of failure.
2. Reduced operating costs
Sensor Fusion can help you lower operating costs by extending the capabilities of devices like UAVs and autonomous robots. As a result, applications such as collision avoidance for inspection drones and remote driver intervention for autonomous transportation systems can utilize low-cost labor centers while also benefiting from remote operations.
3. Increased resistance to attacks
Data fusion and security protocols, including AI, can ensure robust operation of sensor-based systems from malicious attacks (like injecting false signals into input sensors). Among these methods are signal spoofing (e.g., LiDAR and cameras), signal interference (e.g., ABS magnetic sensors, vandalized traffic signs), and side leakage (implanted malware collecting sensitive data).
Edge-device data fusion
The use of Sensor Fusion and AI/ML is moving from centralized data centers to edge devices. There will be three layers of data fusion in future networks:
- Low-level data fusion on smart devices or gateways aggregates sensor inputs.
- Middle-level data fusion supports intensive analytics with a broad range of devices and hub gateways.
- High-level data fusion in data centers or the cloud for a broader system perspective.
Eliminating data voids with Sensor Fusion [Case study]
Data inaccuracy is a primary concern in the malfunction of control algorithms. Sensor Fusion effectively minimizes these information gaps. Another merit lies in making technical decisions based on indirect data. For instance, when it's complex to directly gather information about an object's technical state, we rely on the object's associated behavior. Our experience in this domain is a prime example.
We aimed to enhance an algorithm for a Battery Management System and revise the State Of Health (SOH) estimation for LiFePo4 cells. The SOH of Li-based cells largely depends on their unique chemical properties, which are impossible to gauge without damaging the cell. Therefore, SOH estimation is based on indirect data, some are read instantly with high precision, and others are deduced statistically based on the State of Charge (SOC) or pattern similarity over brief intervals. For real-time SOH estimation of LiFePo4 cells, we analyzed various data types, such as temperature, ohmic resistance, current, and voltage, including voltage spikes and corresponding current surges. This comprehensive analysis, leveraging Sensor Fusion, enabled us to construct a BMS with rapid SOH assessment, as illustrated below. We are open to discussing this further in a demo.
In summary, Sensor Fusion's advantages always revolve around precision and eliminating information voids.
Get your comprehensive guide to a new way to approach BMS—model-based development!
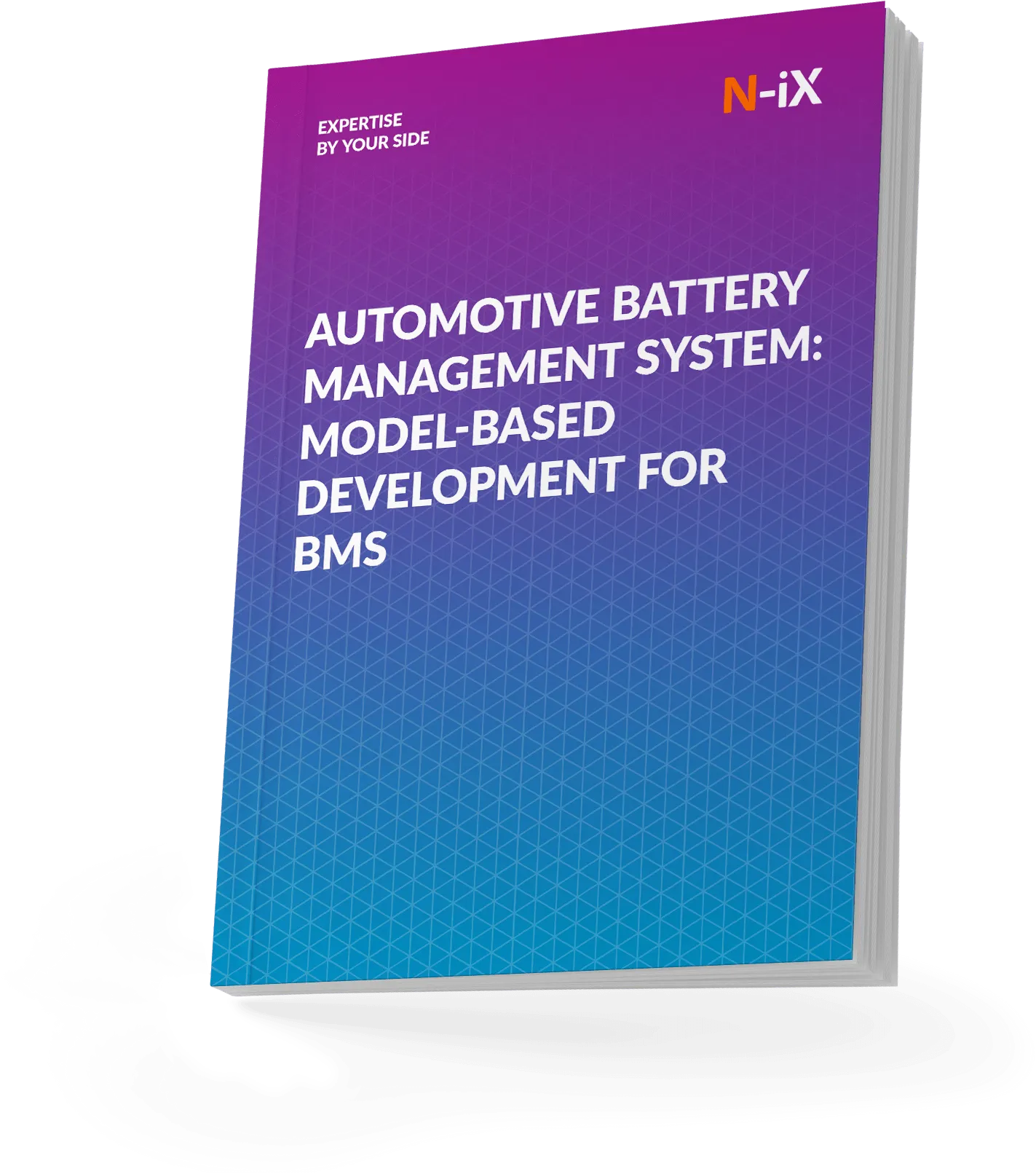
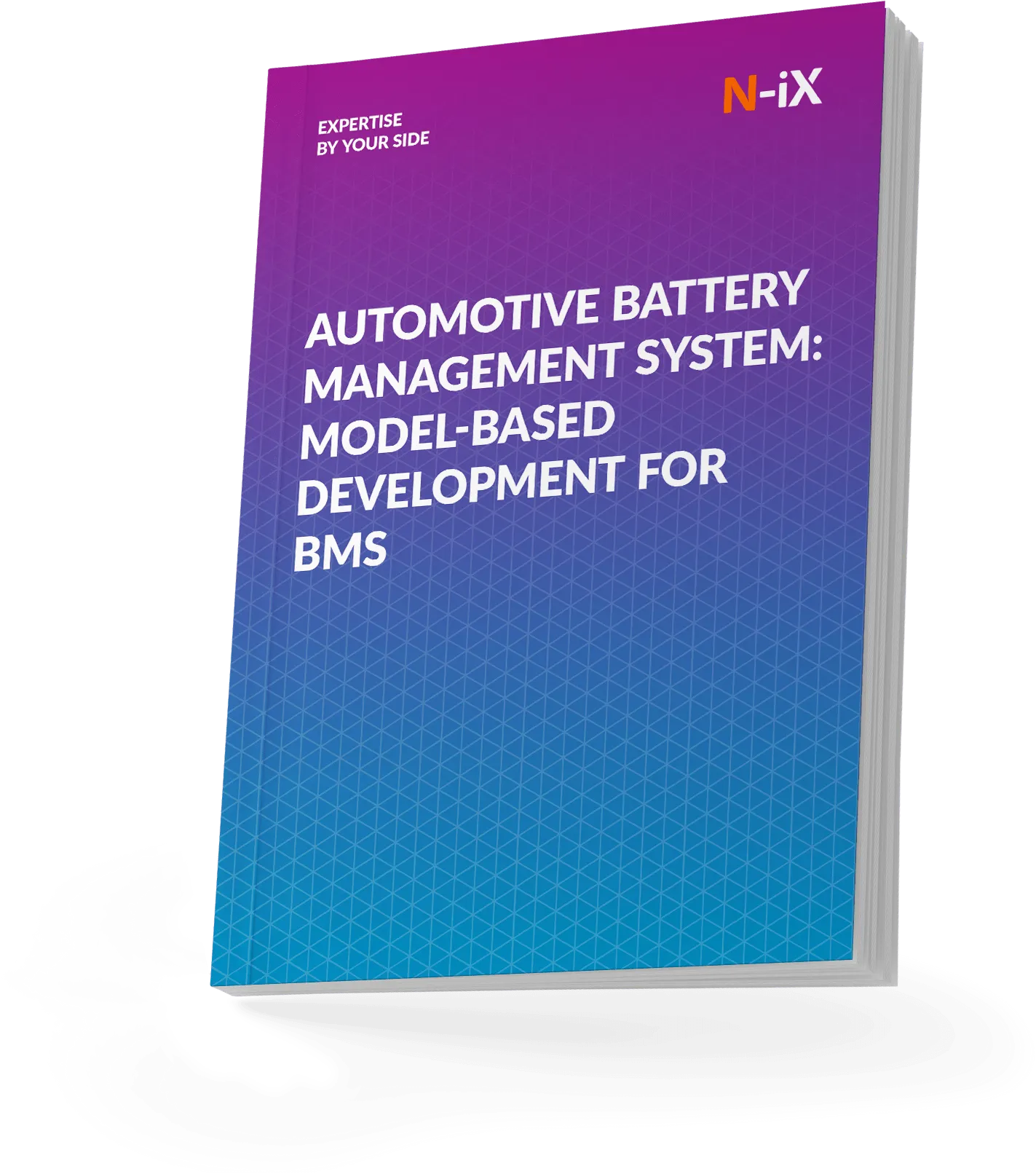
Success!
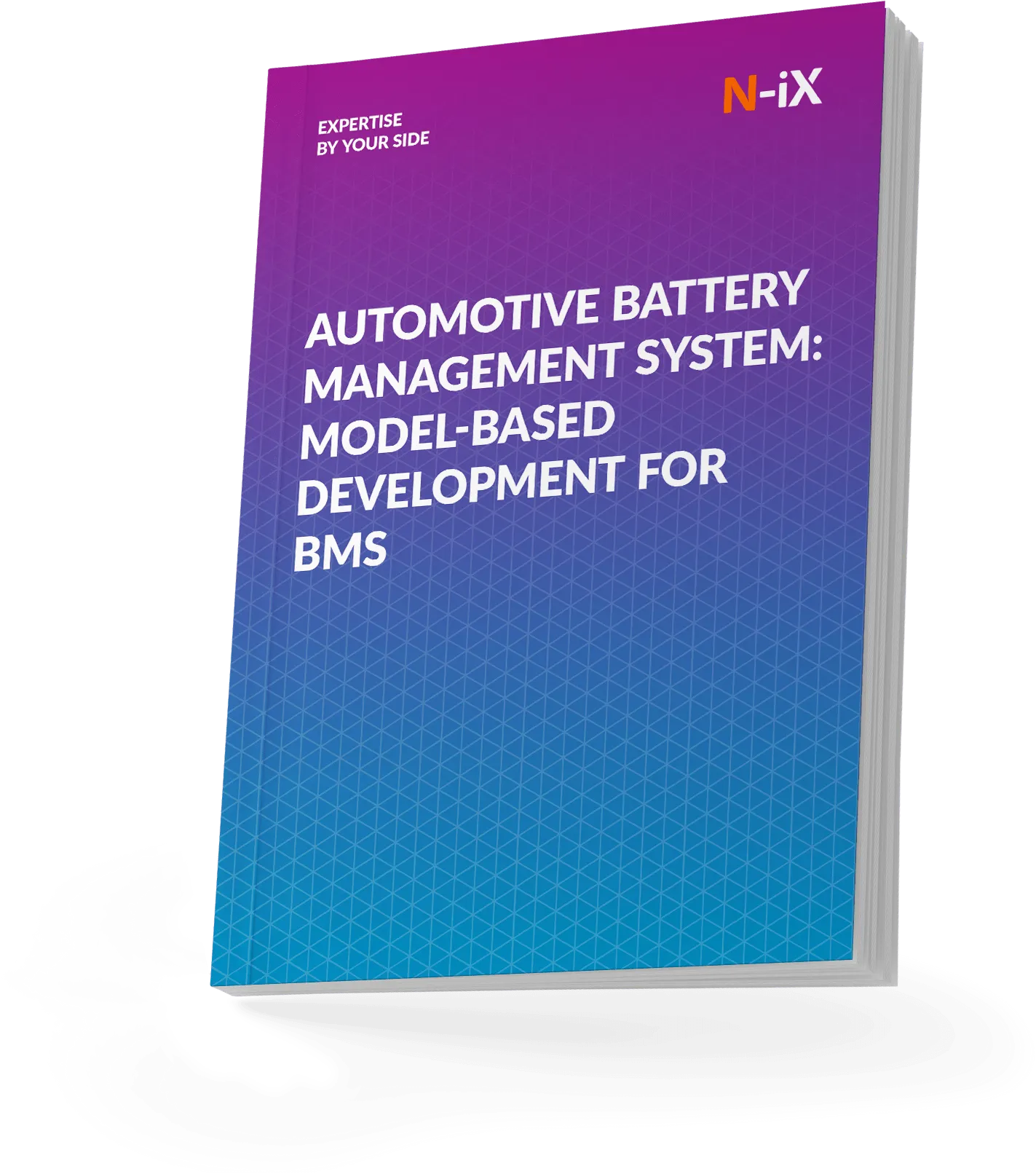
Challenges of Sensor Fusion
There are three primary complexities in fusing data from different sensors. First, there's the issue of varying data accuracy, asynchronous data arrival, and differing signal noise levels. Consequently, they must undergo post-processing to synchronize these signals, as depicted in the first image.
The second challenge in Sensor Fusion is data timeliness, achieving a real-time state. This refers to the stage of actual data deployment, post-processing, and after amalgamating data into an environmental information model.
The third challenge involves mathematical processing. This includes the application of complementary filtering methods, Kalman Filters, and Kiku Filters. Tasks aimed at behavior estimation should incorporate methodologies like Markov Chains, bifurcation point detection techniques, and general forecasting methods.
Using Sensor Fusion techniques to predict vehicle maintenance: N-iX experience in ADAS solutions
Sensor Fusion techniques are one of the methods we employ, depending on the task at hand. Our approach includes manually analyzing and tuning each signal's physical nature for minimalistic program code and using interpolation matrices. We also apply complementary filters (Kalman, Kiku, etc.) for higher accuracy and predictability with lower complexity in fusing the signals. A third option, using machine learning for post-processing and signal parameter synchronization, is currently less suited to the ISO 26262 (Functional Safety) framework, and thus not employed in automotive applications.
Our described experience with BMS was based on the first approach. The second approach was applied to the “Predictability of energy management systems” project, which involved forecasting a vehicle's energy consumption and encompassed a range of environmental, vehicular, and driver data. This solution was unique, combining various environments, data, and systems, and was based on estimating energy costs relative to distance, road type and congestion, ambient temperature, HVAC system consumption, vehicle suspension usage, BMS thermal regulation system, and even the driver's statistical driving style. A generalized data flow diagram processed in this project is shown on the visual below. We are ready to organize a demo if this solution interests you
Who are we, and what can we do for you?
At N-iX, we are leaders in sensor technology and data fusion, using our two decades of expertise in software and engineering services. We specialize in sensor fusion for predictive analytics in automotive and IoT, enhancing Battery Management Systems, and refining control algorithms. Our methods include manual signal tuning, advanced filtering techniques, and machine learning for precision and efficiency.
As your trusted development partner for automotive and IoT products, we offer extensive services from system design to product certification support. Our team has vast expertise in automotive algorithms, battery management, and connected vehicle technology, supported by strong tech partnerships with AWS, GCP, and Microsoft.
Have a question?
Speak to an expert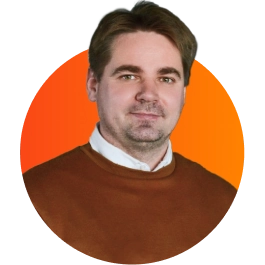