Factory floor processes require efficient, precise, and safe solutions to keep up with production demands, maintain quality standards, and comply with stringent safety regulations. While traditional methods may satisfy these requirements to some extent, robotics in manufacturing can offer improvements beyond human capabilities.
Robots excel in automating repetitive and labor-intensive tasks with precision in processes that require high accuracy. They also significantly enhance workplace safety by handling hazardous materials and performing dangerous tasks, reducing the risk to human workers.
To fully leverage these benefits, factories need to invest in advanced manufacturing software development services. These services power robotic systems and optimize them to reach peak efficiency. Moreover, a trusted tech partner can provide valuable insights on the types of robots to deploy and the best use cases to maximize efficiency. As for now, let us answer the questions that will guide you in implementing robotics on your factory floor.
What are the market trends and future directions in the robotics industry? Which type of industrial robots is required the most? Which technologies drive further development? What are the use cases of robotics in manufacturing? How can a software engineering company empower manufacturers to leverage robotics and automation for improved production processes?
Industrial robotics market overview
The robotics market demonstrates stable and constant growth. According to market.us, it is expected to reach more than $69B in 2025, compared to $60B in 2024. With a CAGR of over 11,4%, it is expected to reach almost $143B in 2032. This consistent growth indicates a strong and sustained demand for robotics solutions across various manufacturing sectors seeking increased automation.
Industrial robot shipments are projected to grow significantly in the coming years. Statista claims that in 2022, shipments amounted to approximately 553,000 units, with only a slight increase from 2021. However, this number is expected to rise sharply, reaching around 718,000 units by 2026. This anticipated growth reflects the rise in the adoption of industrial robots in manufacturing and other sectors.
According to the International Federation of Robotics, there were approximately 3.9M operational industrial robots in 2022, up from 3.4M in 2021. Industrial robots come in a variety of types, including:
- Articulated
- Cartesian
- SCARA
- Collaborative (cobots)
- Parallel (Delta)
The most common type of industrial robot is articulated. Designed to mimic the human arm, these robots offer intricate and precise operations in three-dimensional space. Their rotary joints, ranging from simple two-joint structures to complex ten-joint systems, provide high flexibility and a wide range of motion. This versatility allows articulated robots to perform many tasks, such as material handling, assembly, welding, painting, and more. Given their prevalence and versatility, let's focus on the capabilities and applications of articulated robots.
Top applications of articulated robotics in manufacturing
Achieving success in manufacturing through robotics requires a strategic approach to selecting the most impactful areas for technology integration. This involves aligning robotic systems' advanced capabilities with the company's distinct needs. Moreover, analyzing other businesses' experiences can provide actionable insights. Therefore, based on market.us research, we have arranged the use cases of articulated robotics in manufacturing from the most to the least popular to guide your strategic decision-making.
Material handling
Articulated robots transport, sort, and manage materials with high precision and speed. They take on tasks such as loading and unloading, bin picking, palletizing, and transporting materials, which boosts efficiency, reduces manual labor, and minimizes errors. Combined with Automated Guided Vehicles (AGVs), robotic arms streamline these processes, ensuring smooth material flow throughout the production line and reducing human involvement in potentially dangerous tasks.
Welding and soldering
These processes are critical in sectors like automotive, electronics, and aerospace. Robotic welding systems, including arc welding, spot welding, MIG welding, and laser welding, deliver consistent, high-quality welds with greater accuracy than manual methods. These systems improve safety by minimizing human exposure to hazardous environments. Soldering robots, used in electronics and other precision applications, ensure high productivity and repeatability, with some setups suitable for both small-scale and high-volume production.
Assembling and disassembling
Robotics in manufacturing industry is extensively used to assemble and disassemble a wide range of products and components due to its high precision, speed, and ability to handle heavy components. Assembly robots, often mounted on the floor or an overhead trestle, ensure consistent quality and reduce defects. They perform repetitive operations like fitting, fastening, and screwing with high accuracy. Disassembly robots are employed for tasks such as product dismantling for recycling and rework. Adhesive dispensing robots apply bonding agents during assembly processes, ensuring precise and efficient application.
Palletizing and packaging
Palletizing and packaging are essential manufacturing, warehouse, and distribution center operations. Robotic palletizers stack and organize products onto pallets optimally. These robots can handle various box sizes and weights, using AI to place heavier containers at the bottom and maximize the number of boxes on each pallet. Packaging robots automate numerous tasks, including box forming, filling, sealing, and labeling. They can handle diverse packaging needs, from gently packing food orders and perishable items to assembling and sealing large wire spools into boxes with precision.
Painting
Industrial painting and coating are repetitive due to the consistent size and shape of the parts being painted, making them ideal for robotic automation. Robotic systems ensure high-quality, consistent results and can operate continuously with minimal downtime for maintenance. For instance, automotive manufacturing has been using spray-painting robots for decades. They can maintain a precise distance and speed between the spray head and the workpiece, preventing runs and drips. They accurately regulate pressure and flow to ensure consistent, high-quality finishes.
Milling
Milling, a subtractive manufacturing process, greatly benefits from robotic automation. Robotic milling systems offer high precision and flexibility as well as they can produce complex shapes and detailed features. These robots handle tasks such as drilling, cutting, and shaping materials like metal, wood, and plastic with consistency and accuracy.
Cutting
This application of robotics in manufacturing includes laser, plasma, and waterjet cutting robots, which provide high accuracy and speed for intricate cuts and fine details. Robotic cutting systems are used in industries like automotive, aerospace, and textiles, where precise cutting is essential for producing high-quality components and products. They offer advantages like reduced material warping, improved precision, and enhanced flexibility in cutting operations.
You may also be interested in robotic process automation
Key technologies driving robotics in manufacturing industry
Another consequence of the industrial robotics market growth is the increased demand for the underlying technologies that constitute these advanced systems. This surge in demand creates opportunities for companies specializing in component manufacturing, as well as engineers creating AI/ML algorithms, Computer Vision, Sensor Fusion, IIoT, and Digital Twins.
Artificial Intelligence and Machine Learning
AI and ML algorithms enable robots to continuously learn and improve their performance over time. This intelligence allows for more adaptive and precise operations, enhancing productivity and product quality. AI-driven robots can analyze vast amounts of data, identify patterns, and make autonomous decisions, which significantly reduces downtime and increases operational efficiency.
According to Statista, the AI robotics market will reach $17.03B in 2024, with an impressive annual growth rate of 24.80%, leading to a market volume of $64.35B by 2030. This substantial growth underscores the increasing reliance on AI-driven solutions in robotics.
In manufacturing, AI-powered robots and other complementary technologies optimize supply chains, predict equipment failures, and streamline production processes, providing a substantial competitive edge. For instance, Gartner states that 25% of supply chain decisions will originate from intelligent edge ecosystems by 2025. This shift is largely driven by the adoption of intralogistics smart robots.
Transform your manufacturing processes with AI: Discover key use cases in the white paper!
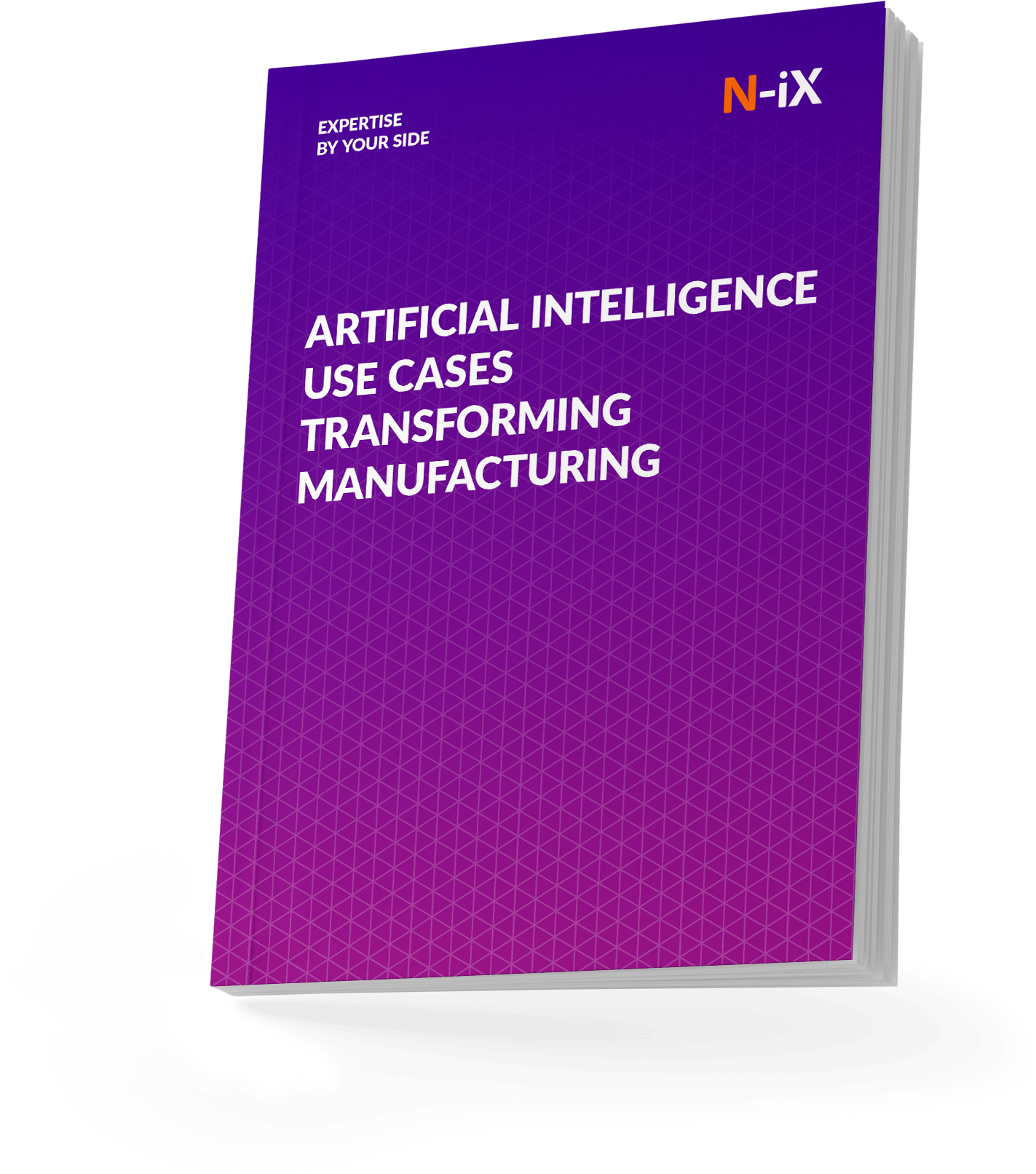
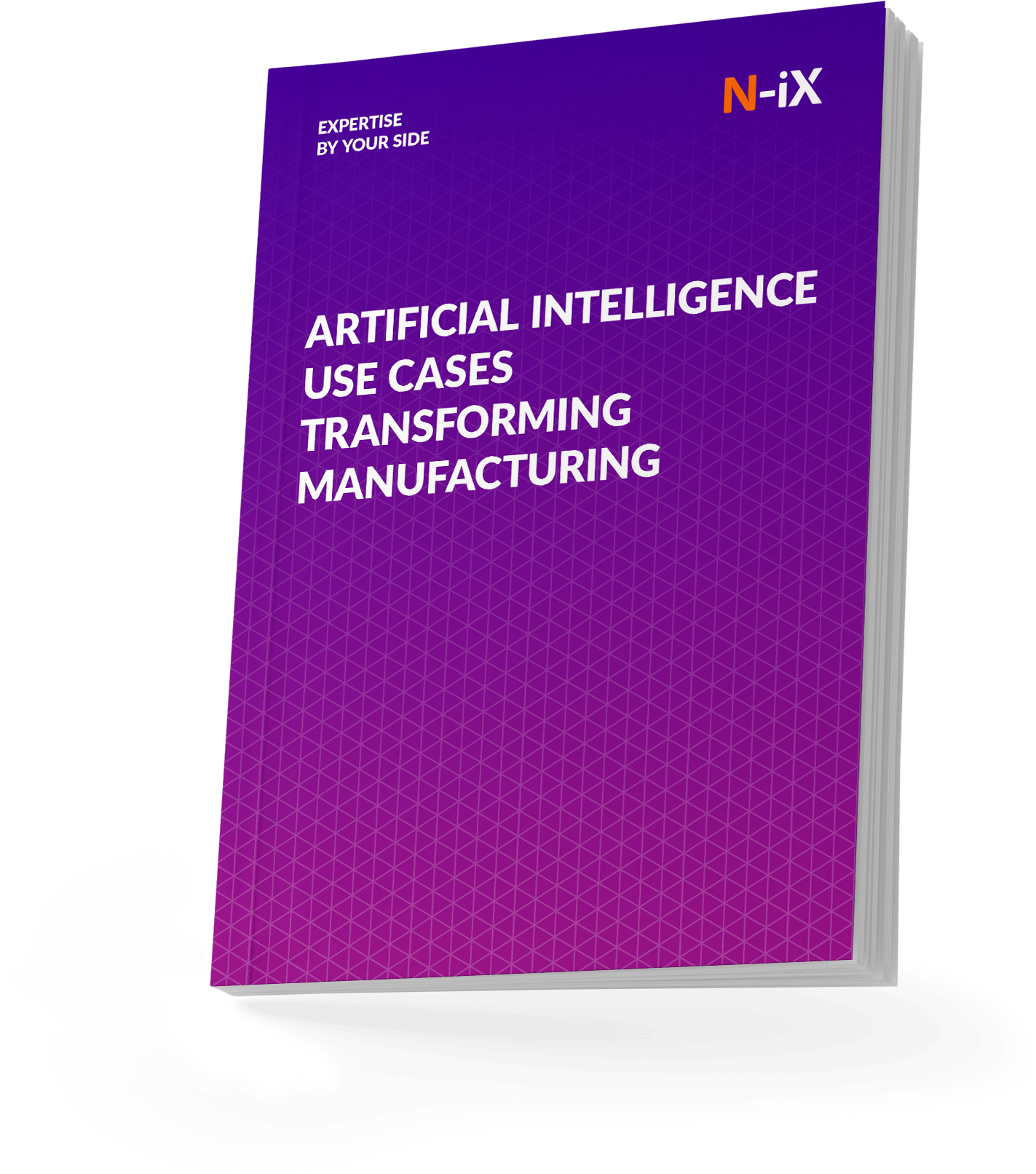
Success!
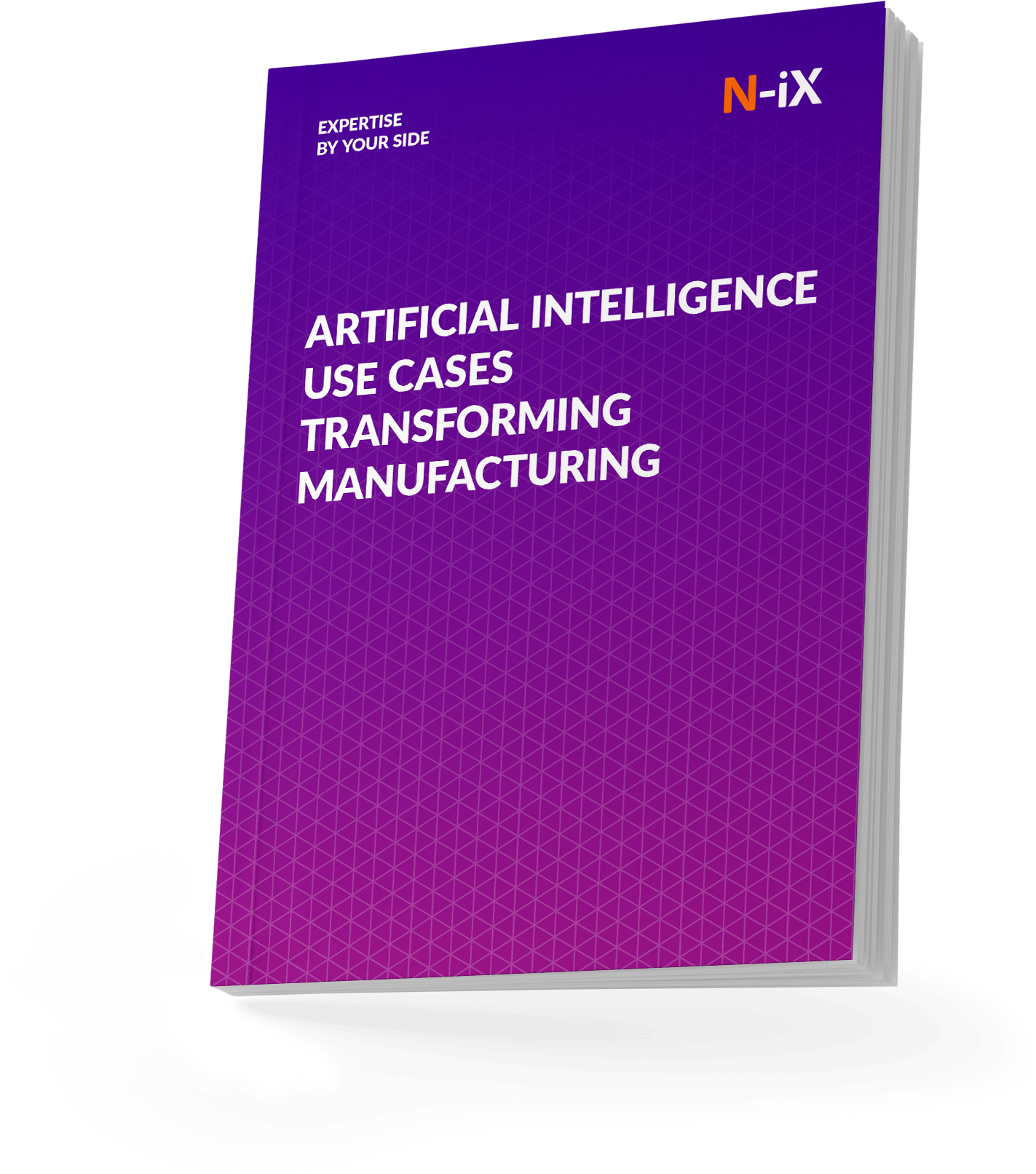
Computer Vision and Sensor Fusion
Robots leverage a variety of sensors and vision systems to perceive their surroundings with high accuracy. A combination of Computer Vision and sensors is crucial for tasks that require fine manipulation and inspection, enabling robots to handle delicate and complex operations.
Computer Vision systems let robots process and interpret visual information from the world around them. These systems utilize advanced image processing algorithms and ML models to analyze visual data helping robots to identify, classify, and respond to objects and events in their environment. High-resolution cameras, coupled with vision algorithms, allow robots to perform such sophisticated tasks as quality control and assembly line operations.
While individual sensors like cameras, LiDAR, and Radar provide valuable data, they are each prone to errors due to wear and tear and environmental factors. To overcome these physical limitations and enhance accuracy, Sensor Fusion was introduced. This approach presumes multiple-sensor data integration, which allows for a more precise comprehension of the environment.
An instance of an application of Computer Vision and Sensor Fusion in robotics could be a robotic arm in a manufacturing plant responsible for assembling small electronic components. This system might use a combination of the following sensors:
- Cameras (for Computer Vision): To visually inspect components and guide the arm's movements.
- LiDAR (for depth perception): To detect the precise position of components in 3D space.
- Force sensors (for touch feedback): To ensure the arm applies the correct amount of pressure when handling delicate components.
These sensors input data into a central processing unit, often referred to as the "data mixer" or "fusion center," which integrates the information to create a comprehensive understanding of the task environment. In this example, the visual data from the cameras is combined with the depth information from the LiDAR and the tactile feedback from the force sensors to precisely position the arm and apply the right amount of pressure.
Actuators, which are the mechanical components of the robotic arm, then act upon this integrated data. The actuators move the arm with precise control to pick up, manipulate, and place components. This combination of sensor data ensures that the robotic arm can perform its tasks efficiently and reliably, even in a dynamic environment where accurate adjustments are constantly required.
Read more about the use of Computer Vision in manufacturing
Industrial Internet of Things (IIoT) and Internet of Robotic Things (IoRT)
A smart manufacturing environment has to be interconnected, which is one of the core purposes of IIoT. In particular, IIoT integrates sensors, devices, machinery, and data analytics to create connected systems that collect, exchange, and analyze data in real time.
Taking a further step, the Internet of Robotic Things (IoRT) specifically concerns robotics, focusing on how robots interact with their environment and other connected devices through the Internet. IoRT enables intelligent, autonomous, and collaborative robotics in manufacturing, significantly enhancing its capabilities and efficiency. Here are the key features:
- Interconnectivity: Robots are equipped with sensors, actuators, and communication interfaces to access the Internet and other devices. This enables real-time data exchange and coordination.
- Autonomous decision-making: IoRT systems leverage data from various sources to make autonomous decisions. For example, a robot in a smart factory can adjust its operations based on real-time data from sensors monitoring production lines.
- Collaborative operations: IoRT enables robots to work collaboratively with other robots and humans. Collaborative robots (cobots) can safely operate alongside human workers, sharing tasks and enhancing productivity.
- Enhanced perception and interaction: Sensor Fusion and Computer Vision systems allow IoRT robots to perceive their surroundings with greater accuracy and effectively interact with their environment.
- Predictive maintenance: IoRT systems continuously monitor the health and performance of robotic components, predicting potential failures before they occur. This practice increases uptime, extends equipment lifespan, and lowers maintenance costs.
- Data-driven optimization: Combining the analysis of real-time data and historical data stored in the cloud, Big Data analytics and Machine Learning algorithms help IoRT systems identify patterns, predict outcomes, and make data-driven adjustments to improve efficiency and productivity.
Discover more about the application of IoT in manufacturing.
Digital twin
A digital twin (DT) is a virtual model of an object, system, or process that is used to simulate, analyze, and optimize its real-world counterpart. In robotics, a DT replicates a robot's physical characteristics, behaviors, and interactions with its environment. This virtual representation is continuously updated with real-time data from sensors and other sources, creating an accurate and dynamic simulation of the robot's operations.
Changes in the digital twin can influence the physical counterpart and vice versa. This bidirectional feedback allows for simulations and adjustments in the digital realm to be tested and then applied to the physical world. Here are some key applications of digital twins in robotics:
- Robot work-cell simulation (RWCS): Using digital twins to simulate robot behavior in a virtual work cell allows for offline programming, testing of robot trajectories, and validation of robot performance before actual deployment.
- Plant maintenance: Remaining Useful Life (RUL) prediction and predictive maintenance benefit from continuous data collection, physics-based modeling, simulation, and analysis empowered by a digital twin.
- DT-aided AI implementations: Digital twins can be used to develop and train robot AI algorithms. This method allows for the simulation of robot behavior in a virtual environment and uses the data collected from the simulation to train the AI algorithms.
- Cloud and edge robotics: When combined with cloud and edge computing, DTs significantly enhance the performance of robotic systems. Cloud computing provides the necessary processing power for complex AI algorithms, while edge computing offers real-time response capabilities for tasks requiring low latency.
Why choose N-iX for robotics in manufacturing?
MATLAB/Simulink Expertise
N-iX offers full-cycle development using both traditional and model-based approaches. Our MATLAB/Simulink experts use visual models to represent system behavior and requirements, which are then automatically converted into code. This approach enhances accuracy, reduces development time, and allows for more rigorous testing and verification.
We have experience in model-based automotive battery management system development and other projects. Moreover, with our dedicated MATLAB/Simulink Academy, we educate new experts in the field to extend our capabilities.
Hardware robotics solutions
Our services include fast PoC, prototyping and manufacturing hardware components, software and firmware solution development, and test automation framework creation.
Our expertise extends to:
- Data acquisition: Read data from various third-party sensors, including those for temperature, humidity, occupancy, vibration, and ambient light, among others.
- Device control: Manipulate a wide range of third-party devices like lighting, heating, ventilation systems, and mechanical components.
- Connectivity: Ensure seamless connectivity to third-party devices using various communication protocols, such as SPI, I2C, UART, and DALI (DALI2).
Robot control systems
Our experts create robot control systems ranging from simple open-loop systems to complex, intelligent systems to satisfy the client's needs. Here’s what we offer:
- Open-loop control systems with predetermined control actions
- Closed-loop control systems that utilize sensor fusion to provide precise and stable operations
- Hierarchical control systems with multi-level decision-making
- Adaptive control systems for environments that require dynamic adjustments to real-time changes
- Intelligent control systems with advanced ML algorithms that enable predictive maintenance, autonomous decision-making, and enhanced human interaction.
We design systems that seamlessly integrate with your existing infrastructure and ensure compatibility with various industrial protocols and standards, including ISO 9001, ISO/SAE 21434:2021, ISO 26262, and ISO/IEC 33020:2019.
Sensor fusion implementation
At N-iX, we have proven expertise in sensor fusion projects. For instance, our experts have developed algorithms for complex systems such as Battery Management Systems (BMS). We analyzed different data types, including temperature, ohmic resistance, current, and voltage, to build a BMS solution with rapid and accurate State Of Health (SOH) estimation for LiFePo4 cells. While this is just an example of how we utilize sensor fusion to enhance system performance, we are open to discussing sensor fusion for robotics in manufacturing in a demo.
Digital twin development
Digital twin technology requires an in-depth understanding of cloud computing, Big Data, AI, and ML. At N-iX, we excel in this area, supported by a robust team of experts. With 400 cloud specialists, including 150 certified cloud experts and 200 data specialists, we have the knowledge and skills necessary to develop and implement virtual replicas of your physical assets, processes, or systems.
Have a question?
Speak to an expert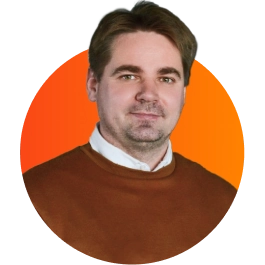