The adoption of robotics in logistics is growing rapidly due to labor cost inflation, workforce shortages, and the need for improved efficiency in supply chains. Robots offer a practical alternative to manual labor by streamlining operations, reducing errors, and enabling continuous workflows. Advancements in Artificial Intelligence and Machine Learning have further enhanced the performance and cost-efficiency of robotics in logistics, making them an essential technology for modern operations. However, successful integration often requires robotics consulting and logistics and supply chain software development to achieve maximum impact.
What are the main benefits of logistics robots for supply chain operations? What are the most common types of robots used in logistics and warehouse automation? What are the primary use cases of logistics robotics? Let’s find out.
Overview of logistics robots market
Precedence research states that the global robotics technology market is expected to grow significantly, reaching $283.19B by 2032. According to Fortune Business Insights, within the logistics sector specifically, the robotics market is projected to grow from $7.11B in 2022 to $21.01B by 2029, with a CAGR of 16.7%. This rapid growth is driven by the rising demand for faster delivery, increased accuracy in order fulfillment, and improved safety across logistics operations.
Robotics has become a vital component of logistics strategies, offering companies a scalable solution to meet growing customer expectations. As the market continues to expand, the future of robotics in logistics promises a significant edge for businesses in the competitive landscape.
Benefits of robotics in logistics
Integrating robotics into logistics operations provides transformative advantages that extend beyond improved efficiency, safety, scalability, and cost-effectiveness. Here are the key benefits of robotics in logistics and supply chain:
Increased efficiency and productivity
One of the main reasons to apply robotics in logistics is that it automates repetitive, high-volume tasks with unmatched precision and speed. Equipped with advanced AI and sensor systems, robots can perform tasks like sorting, picking, and packing at a much faster pace than human workers, ensuring consistent quality and output. Real-time monitoring, predictive analytics, and the ability to operate 24/7 without fatigue further optimize workflows and increase throughput. Moreover, AI-driven systems can analyze incoming data to predict workloads, enabling businesses to allocate resources effectively and minimize bottlenecks.
Improved accuracy
Equipped with advanced Sensor Fusion technologies, robotics offers unparalleled precision in tasks like picking, packing, and sorting. This level of accuracy meets and even surpasses industrial standards, minimizing operational errors and reducing costs associated with returns or inventory mismanagement. Enhanced quality ensures greater customer satisfaction and compliance with industry benchmarks.
Enhanced safety
Automating high-risk tasks significantly reduces workplace incidents, safeguarding employees from injury. Robotics implementation adheres to strict safety guidelines and certifications, guaranteeing compliance with international standards. Certified robotic setups improve workplace safety while mitigating legal liabilities related to workplace accidents, as responsibility often shifts to certified implementers or governing authorities.
Space optimization
Robotics and automation in logistics improve space utilization in warehouses by dynamically analyzing storage needs and item retrieval schedules. Advanced robotic systems optimize placement, considering both physical space and time, placing frequently accessed items and goods scheduled for early dispatch at an accessible distance. Their precision in handling items also reduces the risk of damage, allowing businesses to stack goods more efficiently. Automation further streamlines processes like loading and unloading, improving the flow of operations and maximizing the capacity of existing facilities without requiring expansion.
Potential for non-stop operations
Robotics provides round-the-clock efficiency, serving as an end-to-end solution for logistics. Inside warehouses, robots handle critical tasks like inventory management, picking, packing, and sorting, ensuring seamless operations even during off-peak hours. Outside the warehouse, AI-powered systems enable real-time route planning, autonomous long-distance transportation, and last-mile delivery, adapting to changing conditions such as weather or traffic. Supply chain control towers integrate data from these systems, empowering businesses to make informed decisions, resolve disruptions, and maintain continuous flow.
Cost reduction
Although robotics requires an initial investment, long-term savings are substantial. Robots reduce dependence on human labor and associated expenses like salaries, benefits, and amenities. They also consume less energy, operating effectively in low-light or low-temperature environments, which reduces utility costs. Predictive maintenance further minimizes repair expenses and unplanned downtime, keeping operations running smoothly. Additionally, automation reduces costly errors and accidents, lowering returns, insurance premiums, and potential legal liabilities.
Scalability
Robotics offers unparalleled scalability, allowing businesses to adapt to fluctuating market demands. Modular and adaptive by design, robotic systems can be expanded incrementally to handle increased volumes during peak seasons or when entering new markets. Unlike manual operations, which require significant time and effort to hire and train workers, robots can be deployed rapidly, scaling to meet demand fluctuations without compromising efficiency. Their ability to easily integrate into existing systems also ensures businesses can adjust workflows or add new capabilities.
Discover more about robotics in manufacturing
Key use cases of robotics in logistics
The integration of robotics into logistics is transforming supply chain operations by addressing labor shortages, enhancing operational scalability, and boosting efficiency. The International Federation of Robotics (IFR) reports that over half of all professional service robots sold in 2023 were designed for transportation and logistics applications. Below are key applications of robotics in logistics industry.
Picking and packing
Automated picking and packing systems improve speed and precision in order fulfillment. Advanced vision systems and AI enable these robots to handle diverse products, minimizing errors and optimizing operations. Such systems allow businesses to reduce processing errors and streamline operations in sectors like ecommerce and retail.
Inventory management
Drones and mobile robots automate stock counting and monitoring, providing real-time inventory insights. They reduce manual errors and streamline operations, allowing businesses to improve forecasting and operational planning. Businesses can optimize their supply chain and fulfill orders timely due to identification of stock shortages and overages.
Sorting systems
Automated sorting solutions classify goods based on size, weight, or destination. These systems are essential for courier services and ecommerce fulfillment centers, where high-speed and accurate processing is paramount.
Last-mile delivery
Autonomous delivery robots and drones are reshaping last-mile logistics by addressing urban traffic challenges and lowering delivery costs. Autonomous vehicles navigate sidewalks and airspaces, bypassing traditional traffic congestion and significantly reducing delivery times. They also operate at a lower cost compared to traditional delivery methods, requiring minimal human intervention and fuel consumption.
Palletizing and depalletizing
Robotic systems streamline the stacking and unstacking of goods, improving efficiency and safety in warehouses. By handling heavy or irregularly shaped items with precision, these systems reduce physical strain on workers while increasing throughput.
Automated quality control
Robots equipped with Computer Vision and AI perform real-time quality inspections to detect defects or inconsistencies. These systems ensure adherence to industry standards, reduce returns, and support high-quality production processes in industries such as manufacturing and healthcare.
Read more about Computer Vision in robotics
Warehouse cleaning
Robotic cleaners automate sweeping, scrubbing, and sanitizing tasks, creating a safer and more hygienic environment. Using these robots helps businesses maintain compliance with health and safety regulations without diverting human resources to routine cleaning.
Types of robots used in logistics
Robots in logistics serve diverse purposes, enhancing efficiency across warehouse operations, transportation, and delivery networks. Below are key types of robots widely deployed in the industry.
Autonomous mobile robots (AMRs)
AMRs are versatile robots equipped with sensors, cameras, and AI, enabling them to navigate autonomously. They are used for tasks such as transporting goods within warehouses and facilities, as well as for outdoor operations like delivering parcels in urban or industrial environments. Thanks to their ability to adapt to changing environments, AMRs are well-suited for dynamic and complex logistical tasks, such as navigating around obstacles or responding to real-time demands.
Automated guided vehicles (AGVs)
AGVs use magnetic strips, sensors, or pre-programmed routes to transport heavy loads, pallets, and goods with high precision. They are highly effective for repetitive tasks in warehouses, manufacturing plants, and outdoor logistics hubs such as ports and freight yards. Their reliance on fixed pathways ensures consistent and predictable performance, making them indispensable for operations requiring accuracy and dependability. In settings with heavy traffic, AGVs contribute to organized workflows by minimizing delays and potential collisions.
Collaborative robots (cobots)
Collaborative robots are engineered to work alongside humans, handling tasks such as picking, packing, and moving materials. These robots enhance efficiency in logistics by automating repetitive and labor-intensive activities in warehouses and distribution centers. Cobots are often used for parcel sorting and assembly-line support, where their human-friendly design enables partial automation to bridge the gap between human labor and full automation.
Palletizing and depalletizing robots
These robots automate the stacking and unstacking of items on pallets. Using advanced grippers and vision systems, they precisely handle items of various sizes and weights, reducing the risk of damage during handling. These robots are critical in warehouses, shipping centers, and ports, where they streamline processes such as preparing goods for outbound transport or organizing inbound shipments. Their speed and accuracy significantly lower manual labor requirements while improving overall efficiency in loading and unloading operations.
Sorting robots
Sorting robots classify and organize items based on criteria like destination, size, or priority. They are indispensable in ecommerce fulfillment centers, courier hubs, and distribution facilities, where fast and accurate order processing is essential. By reducing human involvement in sorting tasks, these robots increase throughput and ensure that parcels and shipments are directed to the correct destination. Furthermore, sorting robots enhance the efficiency of the final delivery stage by enabling quicker dispatch of goods.
Drones
Drones are a logistics solution, capable of performing tasks such as inventory scanning, surveying large areas, and completing last-mile deliveries. They excel at reaching remote or hard-to-access locations, such as rural areas or disaster zones, where human-driven delivery methods may be impractical. In logistics hubs, drones are used for real-time inventory monitoring and inspections, providing valuable data on stock levels or site conditions. For small parcel deliveries, drones offer faster and more sustainable alternatives to ground-based transportation, reducing delivery times and operational costs.
Transform your operations with RPA—access the guide to smarter business automation!
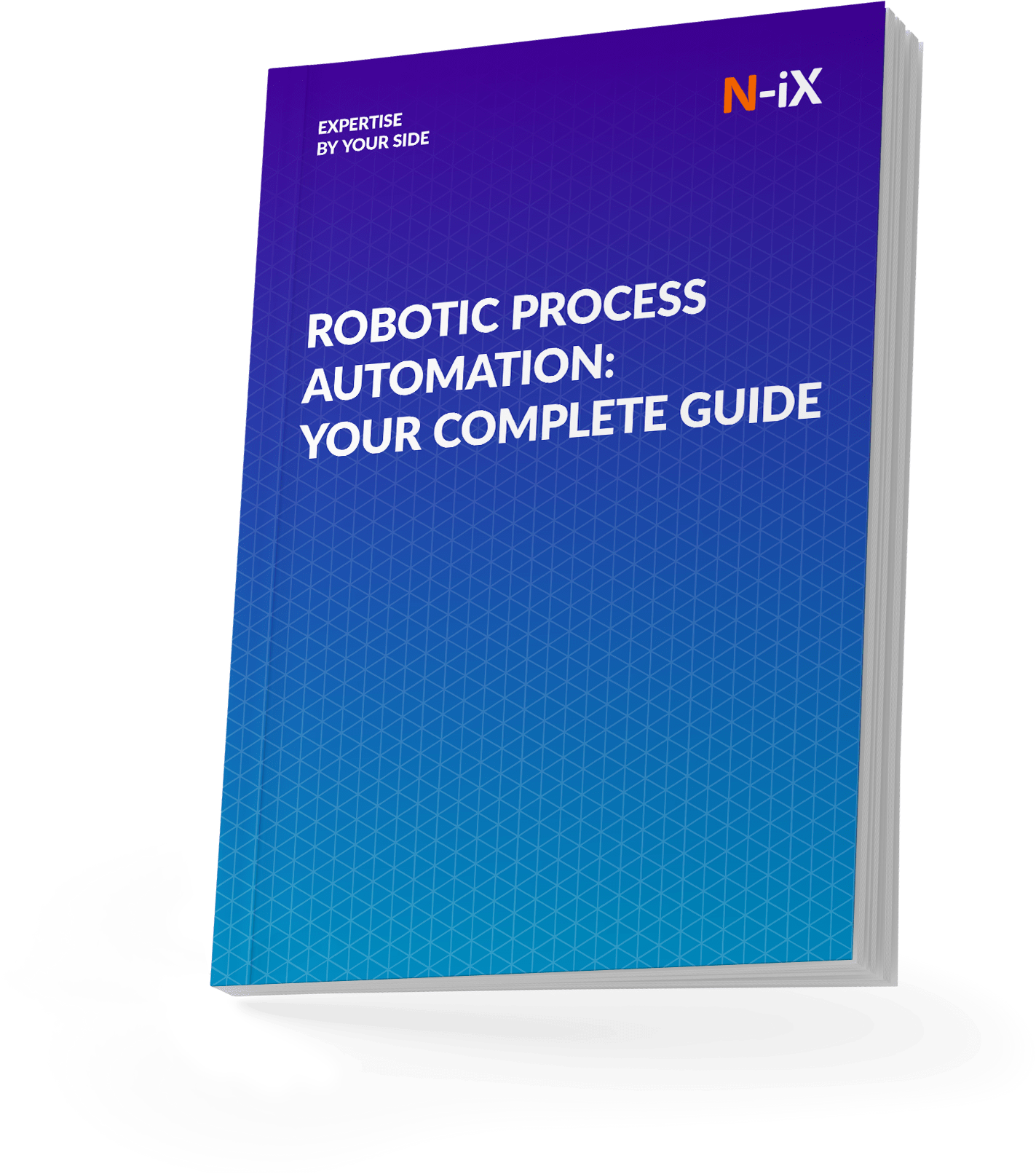
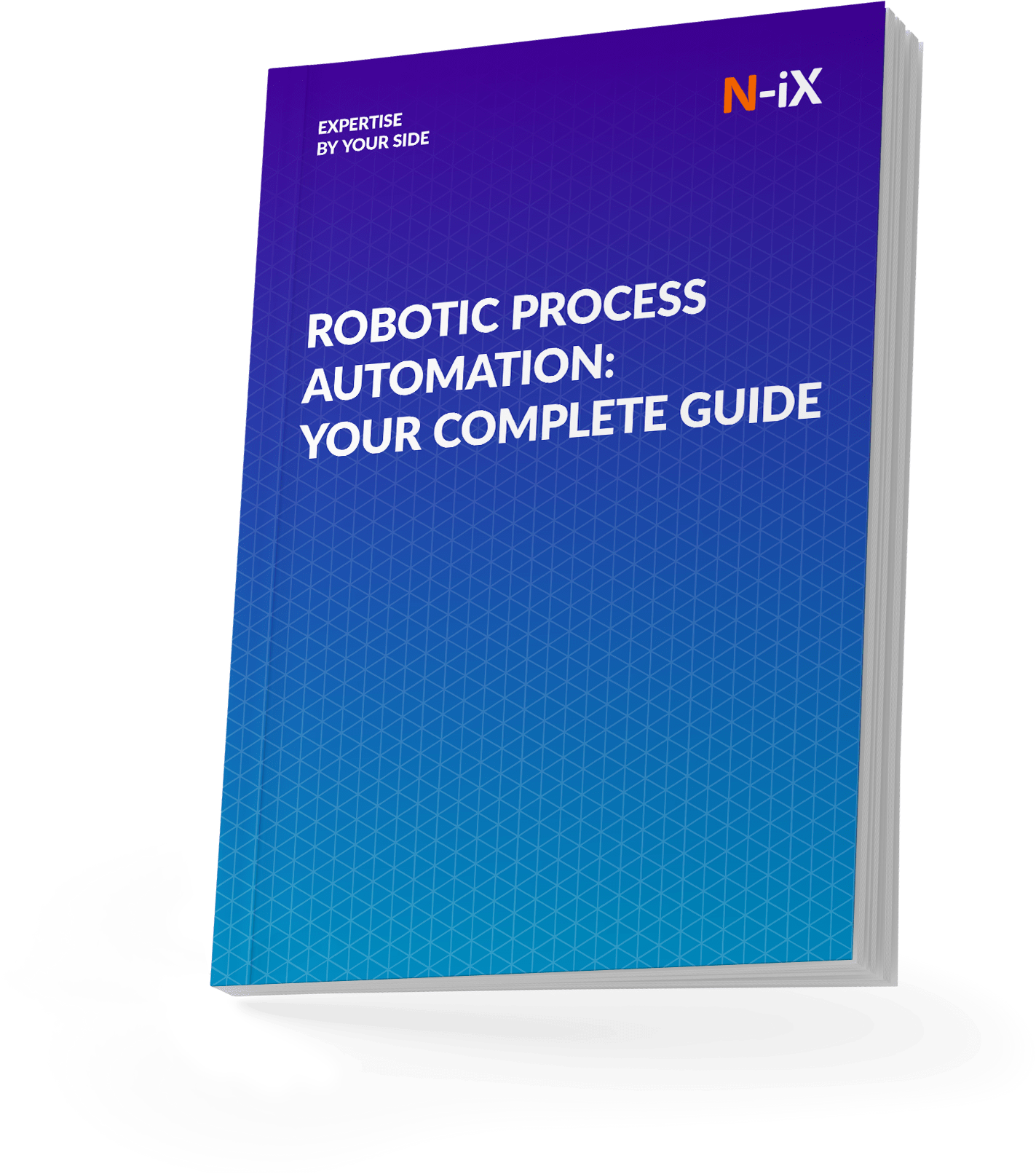
Success!
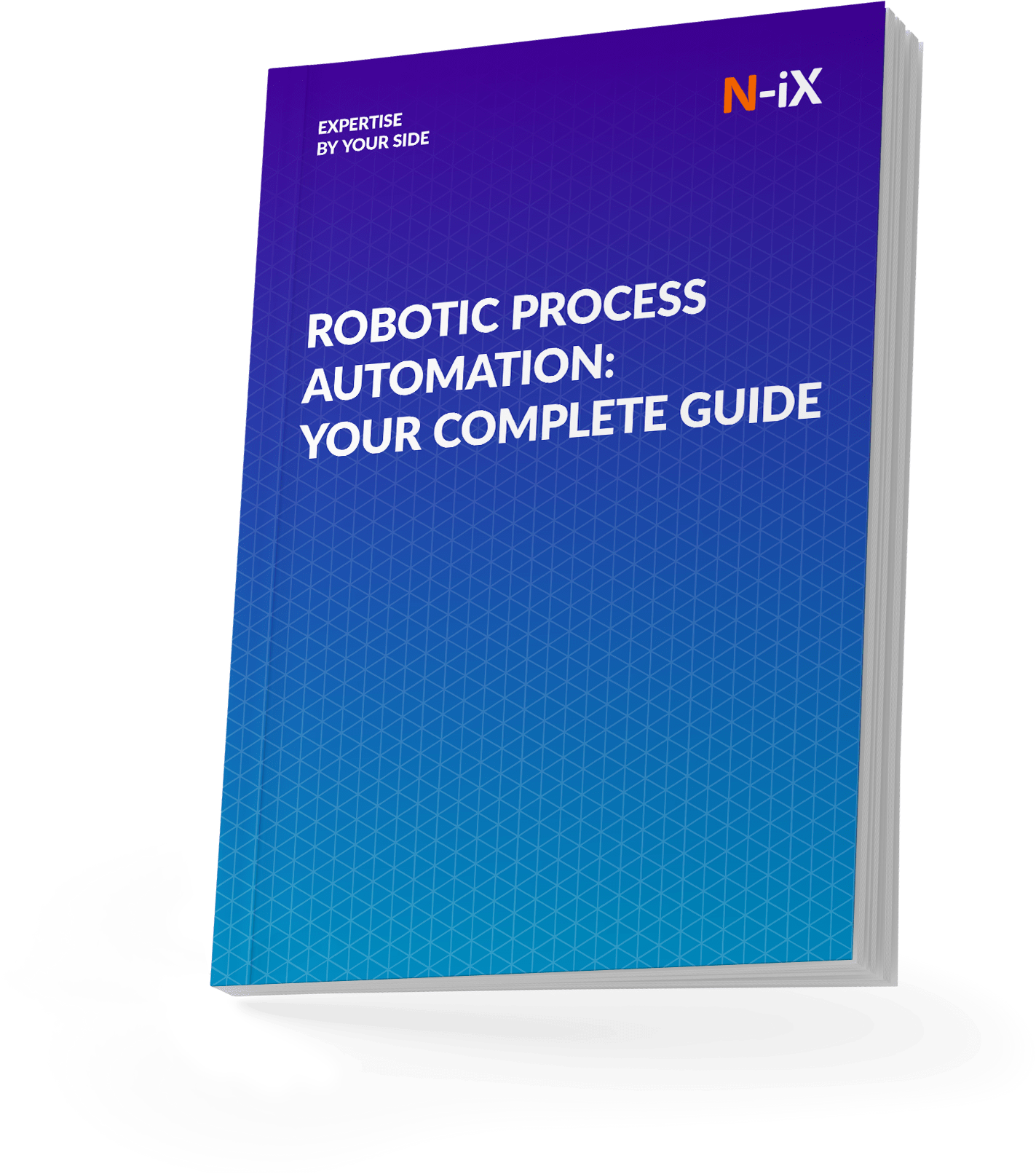
How N-iX implements robotics in logistics
N-iX provides end-to-end support for logistics companies adopting robotics solutions. The process includes five key steps for better efficiency, scalability, and seamless integration into existing operations.
1. Initial assessment
N-iX begins with a comprehensive analysis of your infrastructure and operations. This stage includes reviewing physical spaces, evaluating technological workflows, prioritizing areas for robotic automation, and estimating the financial input required. The goal is to identify high-impact opportunities and define a clear roadmap.
2. Space modeling and process simulation
Our experts visit your facility to perform on-site measurements and build a digital twin—a virtual replica of the space. Using this model, they simulate robotic workflows to assess efficiency, identify bottlenecks, and mitigate risks. The simulation accounts for the unique specifics of the working spaces and production processes, enabling N-iX to experiment with the variables and optimize operations.
3. Transition to robotics
Once processes are optimized, we support the deployment of your robotic solutions. This includes setting up hardware and software, integrating robotics with existing systems, and ensuring minimal disruption to ongoing operations.
4. Stabilization phase
N-iX monitors the system post-implementation to foster smooth operations. During this phase, we fine-tune performance, address emerging issues, and train your teams to work effectively with the new robotics systems.
5. Expansion and optimization
After stabilization, our engineers integrate digital twins from individual systems into a unified operational model. This approach enables comprehensive process management and lays the foundation for scaling robotics to other areas, such as advanced automation or predictive analytics.
Review the best practices for logistics app development
Implementation challenges and how N-iX addresses them
Adopting robotics in logistics presents several challenges that require expert planning and execution. N-iX applies tailored strategies and advanced technologies to address these obstacles.
High upfront costs
Robotic systems often require significant capital investment in equipment, software, and infrastructure. This initial expense can concern logistics companies. However, robotics is a long-term investment that significantly reduces operational costs through improved efficiency, reduced errors, and increased throughput.
N-iX solution: N-iX helps clients minimize financial risks by offering cost-efficient robotics integration strategies tailored to their budgets. Our approach includes prioritizing high-impact areas for automation to maximize ROI and conducting detailed cost-benefit analyses to demonstrate how the investment will pay off over time. Moreover, we assist in designing scalable solutions that allow our clients to expand robotics, gradually spreading costs across multiple phases.
System integration complexities
Integrating robotics into an existing logistics ecosystem is a complex task. Challenges include aligning robotics with legacy systems, preparing workflows for automation, and ensuring compatibility with operational equipment. Mismanaged integration can lead to disruptions in operations, delays, or inefficient processes.
N-iX solution: N-iX addresses integration challenges by conducting a thorough analysis of the existing infrastructure. The process involves:
- Gathering and analyzing operational data;
- Assessing the readiness of workflows, equipment, and personnel;
- Preparing a phased implementation plan to minimize disruptions.
Our experts also integrate customized middleware solutions that enable seamless communication between robotic systems and legacy infrastructure. By aligning technology, processes, and training, engineers from N-iX ensure a smooth transition without interrupting daily operations.
Ongoing maintenance and reliability
Robotic systems require continuous monitoring, proactive maintenance, and performance optimization to avoid unplanned downtime or inefficiencies. Manual maintenance strategies are often reactive and costly, while unreliable systems can lead to operational bottlenecks.
N-iX solution: N-iX builds robust predictive maintenance frameworks using digital twins, AI, and ML technologies. Digital twins—a virtual replica of physical systems—enable real-time monitoring and simulation of robotic processes. AI and ML analyze performance data, predict potential failures, and provide actionable insights to improve system reliability. This proactive approach helps logistics companies reduce maintenance costs, optimize system uptime, and enhance overall operational stability.
Data security risks
The increasing connectivity of robotics systems in logistics introduces cybersecurity vulnerabilities. Risks include data breaches, unauthorized access, and disruptions caused by cyberattacks. Vulnerabilities in these systems may lead to compromised operations and financial losses.
N-iX solution: N-iX implements advanced cybersecurity measures to safeguard connected robotic systems. These measures include:
- Encryption of data transmitted between systems;
- Secure access protocols and authentication mechanisms;
- Regular vulnerability assessments to identify and mitigate potential risks.
By incorporating these cybersecurity practices, N-iX ensures that logistics companies can operate their robotic systems with confidence, even in highly connected environments.
Wrap-up
Robotics has revolutionized logistics, enabling businesses to address workforce challenges, optimize operations, and scale efficiently to meet market demands. Companies implementing robotics in logistics gain significant competitive advantages, from faster order fulfillment to enhanced safety and cost optimization. As robotics solutions continue to evolve, businesses can expect even greater capabilities, fueled by advancements in AI, Machine Learning, and automation. With a clear roadmap, cutting-edge technologies, and robust implementation practices, robotics offers unprecedented opportunities for supply chain optimization.
At N-iX, we combine deep industry expertise with innovative technologies to deliver customized robotics solutions. Our comprehensive approach spans from comprehensive assessment to full transition and scaling. With over 22 years of experience, 2,400 of experts from N-iX bring unmatched expertise to the field. Our engineers enable logistics companies to overcome complex challenges, such as adapting legacy systems, managing workforce transitions, and achieving real-time operational insights. Leveraging the skills of our 200 data experts, we integrate advanced analytics and AI technologies to enhance the efficiency and intelligence of robotics solutions. Our presence in 25 global locations allows us to provide on-site expertise.
Have a question?
Speak to an expert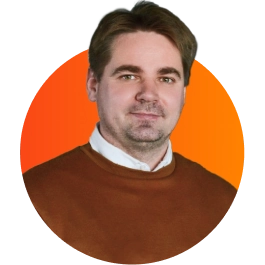