Businesses rely heavily on the efficiency and reliability of their equipment and processes to ensure smooth operations and maximize profitability. Machine downtime and unexpected equipment failures can lead to a significant loss of revenue and even pose safety concerns in critical applications. Predictive maintenance, a proactive approach to equipment management, has emerged as a pivotal strategy to minimize these risks by forecasting equipment failures and analyzing their overall health.
With predictive maintenance machine learning algorithms, it’s possible to improve the accuracy and reliability of maintenance procedures significantly. Keeping that in mind, companies should delve into the importance of machine learning in predictive maintenance and review how algorithms improve the process. Our team will demonstrate a successful machine learning predictive maintenance use case. This way, we’ll highlight the benefits of incorporating machine learning into your asset management efforts.
Why use predictive maintenance & machine learning?
Traditional predictive maintenance approaches rely on fixed schedules, predefined limits, and basic statistical models, often leading to unnecessary maintenance tasks or undetected equipment issues. Organizations can overcome these limitations by utilizing machine learning predictive maintenance algorithms and providing more accurate and effective maintenance solutions.
Here are some key benefits of incorporating machine learning in predictive maintenance:
- Increased accuracy. Machine learning algorithms can build complex models by analyzing and learning from vast amounts of data. These models can predict failures with higher accuracy, ensuring maintenance is performed only when necessary and reducing the risk of unexpected equipment breakdowns.
- Proactive decision-making. Unlike traditional methods, machine learning-based predictive maintenance allows companies to take proactive actions by identifying subtle patterns and trends in equipment behavior. This level of anticipation helps to minimize downtime and optimize maintenance planning.
- Adaptability and scalability. Machine learning algorithms can quickly adapt to new data trends and evolving system parameters, providing a more flexible and scalable solution than static, rule-based approaches.
- Cost efficiency. Organizations can allocate resources more efficiently by accurately predicting the likelihood of equipment failures and targeting only high-risk assets, saving time and maintenance costs.
Adopting predictive maintenance Artificial Intelligence helps companies optimize their asset management, reduce overall operational costs, improve safety, and enhance their brand reputation in the long run.
Read more: IoT based predictive maintenance: use cases
Understanding predictive maintenance machine learning algorithms
Machine learning algorithms can be broadly categorized into supervised, unsupervised, and reinforcement learning. Each type offers unique advantages and is suitable for different Artificial Intelligence predictive maintenance scenarios. Let’s analyze each category and the algorithms most commonly used in predictive maintenance.
Supervised learning
This learning type uses labeled training data to learn patterns and relationships between input features and the corresponding output (e.g., the remaining useful life of a component). These algorithms are handy when a large amount of historical data is available, allowing them to make accurate predictions.
- Regression analysis algorithms, such as linear and ridge regression, estimate the relationship between input features and a continuous output variable. In predictive maintenance, this could involve predicting the remaining useful life of a machine component or the time-to-failure.
- Random forests are an ensemble learning method that constructs multiple decision trees and combines their predictions to improve the overall accuracy and reduce overfitting. This technique is beneficial in predictive maintenance as it can provide insights into the importance of individual input features, enabling organizations to prioritize maintenance tasks accordingly.
- Support vector machines (SVM) algorithms can be used for classification and regression tasks. They work by finding the optimal hyperplane that separates data points from different classes, providing a robust prediction of the remaining useful life or failure probability. SVM algorithms can be particularly effective in handling high-dimensional data, which is common in predictive maintenance applications.
Unsupervised learning
Unsupervised learning algorithms analyze unlabeled data, identifying hidden patterns or structures within the dataset. These algorithms are well-suited for scenarios with limited historical data or rare failure events, making supervised learning approaches less feasible.
- Clustering algorithms. Techniques like K-means clustering or DBSCAN group data points based on similarity or distance measures. In Artificial Intelligence predictive maintenance, clustering algorithms can reveal distinct operational states or failure modes, aiding in root cause analysis and targeted maintenance planning.
- Principal component analysis (PCA). PCA is a dimensionality reduction technique that helps identify the most significant variables while eliminating redundant or irrelevant ones. In predictive maintenance scenarios, PCA can simplify complex datasets, reducing noise and improving the performance of other machine learning algorithms.
Reinforcement learning
Reinforcement learning algorithms, such as Q-learning and Deep Q-Networks (DQN), learn from interaction with their environment to make optimal decisions over time. Though less widely adopted in predictive maintenance than supervised and unsupervised learning techniques, reinforcement learning offers potential benefits. They include optimizing maintenance schedules and policies by continuously adapting to the system's evolving conditions.
By understanding and leveraging the strengths of each machine learning algorithm category, organizations can develop highly effective predictive maintenance AI models that meet their specific needs and requirements, ultimately improving asset management and reducing operational costs.
A note on data collection and processing
For any predictive maintenance program to be successful, data is the foundation. High-quality data enables machine learning algorithms to learn and make accurate predictions, driving the effectiveness of the entire process. Thus, understanding the importance of proper data collection and processing techniques is essential for organizations adopting machine learning-powered predictive maintenance AI solutions.
Importance of data quality
Machine learning algorithms can only be as reliable as the data they are trained on. Accurate, complete, and consistent data is crucial to attaining high-performance predictive models that deliver actionable insights. Several factors contribute to data quality, including data from various sources (sensors, historical records, maintenance logs), high-resolution measurement intervals, and the inclusion of normal operating conditions and failure events.
Data sanitization and preprocessing
Before feeding the data to machine learning algorithms, your tech vendor has to perform several preprocessing steps to ensure data quality and model performance. These preprocessing steps include:
- Data cleaning - removal of outliers, handling missing or corrupted data, and addressing discrepancies in the dataset.
- Data normalization - scaling or transforming the data to fit within a standard range or distribution, minimizing the influence of unrelated factors on the analysis.
- Data integration - combining data from disparate sources into a coherent dataset, ensuring consistency and compatibility among the data types and formats.
At N-iX, our Data unit specialists will handle all data sanitization and preprocessing procedures, including cleaning, normalization, and integration. With our expertise, you can expect the work to be delivered to proceed with predictive maintenance initiatives of your organization.
Feature engineering for predictive maintenance
Feature engineering is the process of creating new input features or transforming existing ones to improve the performance of machine learning algorithms. In predictive maintenance, feature engineering might involve extracting statistical features (such as the mean, median or standard deviation) from a time series, calculating aggregate metrics or changes over time, or generating frequency-domain features using techniques like Fourier transform or wavelet analysis.
Practical feature engineering can significantly enhance the accuracy of predictive maintenance AI models, enabling organizations to detect subtle patterns and trends that indicate potential equipment failures. It also helps reduce datasets' dimensionality, improving algorithms' efficiency and computational performance.
Proper data collection and processing lay a solid foundation for predictive maintenance models, allowing organizations to boost asset performance, reduce downtime, and achieve significant cost savings.
Read more: Using big data analytics for predictive maintenance: how enterprises slash downtime
Challenges and limitations of predictive maintenance machine learning
While machine learning-driven predictive maintenance offers numerous benefits, it is essential to understand the challenges and limitations associated with its implementation. By acknowledging these hurdles, organizations can take appropriate steps to address them and ensure the successful integration of machine learning solutions into their maintenance strategies.
1. Data privacy concerns
Data protection and privacy are critical concerns in the age of digitalization. As machine learning algorithms rely on vast amounts of data, organizations must comply with data privacy regulations, such as GDPR, when collecting and processing data for predictive maintenance. Your tech vendor has to ensure proper data handling practices, anonymize sensitive information, and employ secure data storage solutions. These options can help organizations safeguard privacy while harnessing the power of machine learning.
2. The complexity of algorithms and model explainability
Machine learning models, especially deep learning ones, can be highly complex, making it challenging for non-experts to understand the underlying reasoning behind predictions. This lack of transparency may result in reluctance from stakeholders to rely on these models for critical maintenance decisions. To address this issue, organizations can partner with a global vendor with sufficient investment in research and development of explainable AI (XAI) techniques.
3. Hardware and computational requirements
Machine learning algorithms often require significant computational resources for training and making predictions. Organizations must carefully consider their hardware infrastructure requirements and explore options such as distributed computing, GPU acceleration, or Cloud-based solutions to meet the computational demands of these algorithms cost-effectively.
Despite these challenges, the potential benefits of machine learning-based predictive maintenance outweigh the limitations. By proactively addressing these concerns by cooperating with a credible tech partner, organizations can effectively harness the power of machine learning to optimize their predictive maintenance strategies. In turn, it allows for reducing operational costs and maintaining the industry's competitive edge. The good thing is that partnering with a global software solutions and engineering services company that delivers solutions boosting business value is absolutely recommended. At N-iX, predictive maintenance specialists can help mitigate the indicated challenges by ensuring proper data handling practices, offering Data expertise, and delivering Cloud solutions.
The success story of predictive maintenance Artificial Intelligence for flawless operations
Gogo is a global provider of in-flight broadband Internet with over 20 years of experience and more than 1,000 employees. The company's superior technologies, best-in-class service, and global reach help planes fly smarter, airline partners perform better, and their passengers travel happier.
Gogo needed to improve the quality of the in-flight Internet. Its satellite antennas often malfunctioned, leading to paying penalties to the airlines. We helped Gogo migrate its on-premise data solutions to the Cloud to process a considerable amount of data from over 20 sources. The migration to AWS Cloud expanded data processing capacity, saved on licenses and on-premise infrastructure, and allowed for the development of a Cloud-based unified data platform.
Then, using Data Science and Machine Learning algorithms, our team developed predictive maintenance models for forecasting satellite antenna failures and health monitoring. The solution delivered interpretable reasoning behind each recommendation.
Value delivered:
- Migration to the Cloud allowed Gogo to minimize expenses on licenses (Cloudera/Microsoft) and on-premises servers while allowing them to efficiently manage and allocate resources in the Cloud according to their processing requirements;
- The implementation of predictive maintenance machine learning algorithms led to a 75% reduction in no-fault-found (NFF) cases, generating savings by avoiding unnecessary equipment servicing;
- Predictive maintenance Artificial Intelligence facilitated antenna failure prediction with over 90% accuracy 20-30 days beforehand, ensuring in-flight equipment servicing occurs during optimal times, such as when no flights are scheduled for a plane;
- By pinpointing causes behind poor antenna performance (e.g., antenna failures resulting from the use of antifreeze fluid), Gogo was able to mitigate typical failure factors, such as adding an extra protective layer to the antennas.
Final remarks
Predictive maintenance approaches have opened up new pathways for organizations to optimize asset management strategies and achieve significant cost savings. By emphasizing the advantages of such solutions, organizations investing in these advanced tools will prove worthwhile in the long run, providing them with a competitive edge and increased profitability.
As the technology continues to evolve, the potential for machine learning-based predictive maintenance is immense. Organizations consider partnering with predictive analytics consultants to explore and leverage these advanced solutions to stay ahead of the competition while continuously working to address the inherent challenges. By doing so, companies can unlock the full potential of machine learning-driven predictive maintenance, ensuring optimized asset performance, minimized downtime, and maximized return on investment.
Why choose N-iX for Predictive maintenance Artificial Intelligence implementation?
- N-iX is a global provider of AI, ML, and Data Science with more than 22 years of experience in data-related services;
- The company boasts a team of over 200 data professionals who are experts in various fields such as data visualization, Business Intelligence, AI/ML, Data Analytics, and Data Analytics strategy;
- The company has a diverse portfolio of clients in the Data services sector, including cleverbridge, Discovery, Lebara, AVL, Orbus Software, Gogo, and a range of Fortune 500 companies;
- N-iX has been consistently recognized by CRN as a leading solutions provider in North America, as evidenced by their Solution Provider 500 and CRN Fast Growth 150 ratings;
- The company adheres to industry regulations and standards such as PCI DSS, ISO 9001, ISO 27001, and GDPR.
Have a question?
Speak to an expert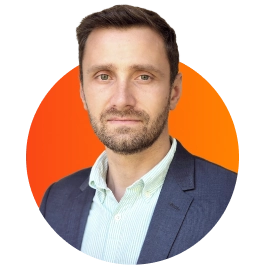