As vehicles become more connected and intelligent, the role of software is expanding far beyond traditional control systems. Today, automotive software development powers core functions like driver assistance, energy optimization, and remote diagnostics. IoT in the automotive industry plays a central role in enabling real-time data exchange between vehicles, infrastructure, cloud platforms, and edge systems.
Building such systems requires more than embedded expertise. Delivering secure, scalable, and standards-compliant solutions calls for strong capabilities in cloud integration, AI/ML, and system interoperability. Partnering with an experienced IoT development company helps accelerate delivery, reduce risk, and ensure long-term adaptability in a fast-moving market.
What are the IoT use cases in the automotive industry? What are the real-life examples of its implementation? How to mitigate the challenges associated with the implementation? Let’s find out.
Use cases of IoT in the automotive industry
The impact of IoT in the automotive industry is most evident in its practical applications across vehicles and infrastructure. Below are the key use cases that demonstrate how connected systems enhance safety, efficiency, and real-time decision-making.
Connected vehicles
IoT applications in the automotive industry introduce real-time communication between the vehicle and its surrounding environment. This connectivity supports various interactions that contribute directly to road safety, traffic efficiency, and user convenience.
- Vehicle-to-vehicle (V2V) communication lets cars exchange information about their position, speed, braking activity, and movement intentions. When two vehicles approach an intersection or travel closely at high speeds, embedded IoT sensors in automotive systems reduce collision risks by alerting drivers or initiating automated responses.
- Vehicle-to-pedestrian (V2P) technology improves safety in urban areas and low-visibility zones. Vehicles identify nearby pedestrians through IoT-enabled smartphone signals or wearable devices. If someone is about to cross unexpectedly, the system warns the driver or intervenes by slowing down.
- Vehicle-to-infrastructure (V2I) communication connects the car to traffic lights, parking systems, toll booths, and other road assets. IoT communication protocols such as DSRC or 5G allow vehicles to receive signal timing data to adjust speed for fewer stops, reducing fuel consumption. V2I also supports car-sharing services by coordinating pick-up/drop-off locations and optimizing vehicle availability.
- Vehicle-to-everything (V2X) extends communication to broader environmental elements. Systems gather visual and sensory input from the surroundings, such as traffic signs, road conditions, and objects on the road. IoT-connected vision systems and roadside sensors allow vehicles to process this data in real time to classify the driving context and make informed navigation decisions. These capabilities highlight a key domain of IoT in automotive safety systems, where timely responses reduce the likelihood of collisions.
Together, these functions support the transition toward software-defined vehicles. Instead of relying on hardware updates alone, manufacturers can introduce new features or fix issues remotely through over-the-air updates. Electronic control units (ECUs) located across the vehicle handle distributed processing and allow quick response to incoming data, reducing latency and improving reliability.
Autonomous vehicles
Autonomous driving depends on seamless coordination between sensors, onboard computing systems, and external data sources. IoT in automotive systems connects data streams from cameras, LIDAR, radar, and ultrasonic sensors. These inputs support core functions such as object detection, path planning, and motion control.
A modern autonomous vehicle processes data at multiple layers. Local ECUs manage narrow tasks such as pedestrian recognition or lane detection, while a central processing unit fuses these inputs into a driving decision. Within the automotive IoT stack, this structure helps reduce latency and enables vehicles to act on information beyond their sensor range, drawing additional data from nearby connected vehicles or infrastructure.
Autonomous vehicles are constantly upgraded to operate safely in more complex conditions, such as unstructured roads or mixed traffic environments. Businesses that deploy autonomous systems gain measurable benefits: lower labor costs, fewer collisions, and improved service availability in logistics, ride-hailing, and delivery use cases.
However, while manufacturers work on higher levels of autonomy, as of 2025, only levels 0 through 4 are technically and commercially viable. Here is a breakdown of the classification by the extent of driver involvement required:
Predictive maintenance
IoT in the automotive industry supports predictive maintenance by continuously tracking the condition of critical vehicle components in real-world operating environments. Sensors installed across systems, such as the engine, braking, battery, and tires, measure variables like temperature, pressure, vibration, and voltage. These inputs provide a real-time view of system health and allow early detection of anomalies that indicate wear or performance degradation.
When the system identifies abnormal behavior, such as elevated friction in braking systems or unexpected power draw from the battery, it automatically triggers alerts or schedules inspections. Maintenance workflows shift from reactive repairs to planned interventions based on actual usage patterns and condition-based thresholds. This approach reduces the risk of on-road failures and avoids unnecessary service downtime.
According to Global Trade Magazine, predictive maintenance can lower overall maintenance costs by 30% to 40% compared to traditional reactive maintenance. Vehicle owners experience fewer service interruptions and better reliability. Service providers optimize resource planning, reduce waste, and extend vehicle availability. For OEMs, access to aggregated sensor data enhances product quality tracking, supports warranty validation, and accelerates engineering feedback loops.
Fleet management
Managing a fleet of vehicles requires accurate, real-time visibility into operations, a capability provided by implementing IoT in the automotive industry. Automotive IoT systems track location, route adherence, fuel consumption, engine health, driver behavior, and other metrics. These inputs feed into cloud-based fleet management platforms that generate alerts, reports, and optimization suggestions.
ECUs installed in fleet vehicles allow for deeper integration between hardware signals and operational platforms. Data collected at the vehicle level supports precise diagnostics, remote firmware updates, and compliance monitoring.
For example, if a driver exhibits harsh braking or frequent idling, fleet supervisors receive notifications and can provide feedback to reduce wear and fuel waste. Vehicles operating outside geofenced areas trigger alerts that prevent unauthorized use or potential theft.
With full visibility into operations, logistics companies and mobility providers make better decisions about route planning, asset utilization, and risk management. They also reduce insurance premiums by demonstrating safe driver behavior backed by IoT data.
Advanced driver assistance systems (ADAS)
ADAS features rely on IoT to deliver real-time feedback and automation that directly improve driver performance and road safety. Here is how IoT in the automotive industry enhances core ADAS functions:
- Driver monitoring systems observe eye movement, head position, and alertness levels. If the system detects fatigue, distraction, or drowsiness, it warns the driver or adjusts vehicle behavior. In fleets, these systems reduce the risk of accidents related to driver impairment while also contributing to regulatory compliance in some jurisdictions.
- Traffic prediction systems analyze vehicle telemetry, road conditions, and external traffic data to identify patterns of congestion. Drivers receive rerouting suggestions based on predictive analytics, which helps shorten travel time and improve fuel efficiency.
- Road condition analysis and navigation assistance use onboard cameras and vehicle-to-infrastructure data to detect potholes, slippery surfaces, and construction zones. The vehicle adjusts its speed and trajectory, and in some cases, shares this information with other vehicles to improve overall traffic safety.
Each ADAS feature runs on a software-defined architecture, which allows manufacturers to update and improve system behavior over time. Automakers can enhance algorithms, introduce new features, or comply with changing safety regulations through software updates. The modular design of ECUs allows for activating different levels of ADAS functionality depending on the vehicle model or the customer’s subscription tier. This flexibility supports new revenue streams, such as feature-on-demand or post-sale upgrades.
IoT in automotive systems: Case studies by N-iX
Predictive energy management for electric vehicles
A European EV manufacturer partnered with N-iX to develop an intelligent energy management system driven by in-vehicle IoT telemetry. The system connects multiple subsystems, such as powertrain, HVAC, and suspension, through embedded control units that collect and process real-time data from vehicle sensors, including battery state, road conditions, and driver behavior.
Our engineers applied an interdisciplinary approach rooted in robotics system design. The architecture follows a ROS-inspired node structure, where each ECU operates as a functional node responsible for localized processing. A central control module orchestrates the system by issuing directives to individual nodes based on aggregated data and predictive algorithms.
N-iX implemented this architecture using Simulink, Embedded Coder, and AUTOSAR Adaptive, deploying lightweight models to embedded hardware. The result is a fully distributed yet coordinated IoT system that optimizes energy consumption in real time without relying on cloud connectivity.
Explore the whole case on predictive energy management for EVs
Expanding battery management analytics to embedded platforms
A global provider of battery diagnostics solutions engaged N-iX to migrate its analytics engine from a centralized cloud infrastructure to a distributed, vehicle-embedded IoT architecture. The objective was to enable real-time battery health monitoring on microcontroller-based systems with constrained resources.
Our team re-implemented the algorithm in C and optimized it for execution on low-power ECUs. Each battery module now transmits real-time telemetry—voltage, temperature, charge/discharge cycles—directly to an embedded diagnostics layer within the vehicle. This localized processing architecture allows the system to detect anomalies at the cell level, issue early warnings, and operate independently of cloud availability. The new architecture significantly reduces latency, bandwidth usage, and dependency on remote diagnostics infrastructure.
Read more on how we expanded battery management services to embedded systems
Challenges of implementing IoT in the automotive industry and solutions by N‑iX
As vehicles become increasingly connected and software-defined, the rise of IoT in the automotive industry introduces a new wave of engineering and operational challenges. These challenges include safeguarding cyber-physical systems, processing complex real-world environments, and integrating connected vehicles with inconsistent infrastructure. At N-iX, we combine deep expertise in automotive-grade cybersecurity, embedded AI/ML, and scalable IoT platforms to help our clients overcome these challenges and build future-ready solutions.
Securing every layer of connected vehicle systems
Every connected vehicle introduces a complex threat surface that spans hardware, firmware, communication protocols, and backend systems. Weaknesses at any level—whether on the device, in the communication layer, or in the cloud—can compromise safety and trust.
We implement security frameworks that cover all layers of the architecture. Our solutions adhere to ISO 21434 and ISO 26262 standards to ensure both cybersecurity and functional safety. We build secure OTA update mechanisms, encrypted ECU communication channels, and protected device identities.
Moreover, our engineers are experienced in using blockchain-backed SIM technology to support decentralized, tamper-resistant authentication. These approaches allow connected vehicles to securely verify identities and exchange trusted data with other vehicles or roadside infrastructure without relying on centralized servers. The result is a more resilient and secure V2X environment, an essential requirement for scaling IoT in the automotive industry.
Read more about IoT connectivity and how to build a reliable network
Making vehicles context-aware in complex, uncertain environments
Sensors can fail to capture complete information due to poor weather, obstructions, or sensor interference. Autonomous features must still function safely even when inputs are partial or noisy.
We address this challenge using a flexible sensor fusion architecture that combines multiple data streams, such as LIDAR, radar, cameras, and ultrasonic sensors, into a unified perception layer. In such a way, the vehicle can maintain situational awareness even when some sensors underperform.
To support rapid and adaptive decision-making, we design and integrate dedicated AI/ML processing nodes directly into embedded or edge systems. These modules run real-time inference for tasks like object classification or trajectory prediction. Our team integrates low-power, high-performance processors that can handle edge intelligence with minimal latency.
Where applicable, we build mesh network architectures that allow vehicles and edge nodes to share critical data locally. These architectures improve redundancy, maintain functionality during partial connectivity, and ensure low-latency responses to dynamic changes in the environment.
Integrating vehicles with existing infrastructure
Many road networks are not yet optimized for connected vehicle deployment. Gaps in network coverage, outdated roadside equipment, and limited standardization make consistent V2X communication challenging to achieve.
We help our clients overcome these limitations through flexible connectivity solutions. Our teams design adaptive communication systems that maintain performance across modern and legacy environments. We work with low-latency wireless protocols, resilient edge-cloud data flows, and dynamic switching between local and centralized systems.
Where connectivity is unstable or infrastructure is outdated, we implement hybrid architectures that shift computing between the vehicle and the cloud depending on real-time network conditions. In such a way, key functions remain available, even in rural or underdeveloped regions.
Why should you choose N-iX for IoT applications in automotive?
- Proven IoT delivery expertise: More than 22 years of experience building full-scale IoT solutions, from connected sensors and edge processing to cloud platforms and secure device management;
- Secure V2X communication with blockchain: Competency in blockchain-backed SIM technologies for decentralized, tamper-resistant authentication across vehicle networks;
- Over 200 AI/ML specialists: Strong in-house data science and ML engineering teams delivering real-time analytics, predictive models, and embedded intelligence;
- Compliance with automotive standards: Expertise in ISO 26262, ISO 21434, and ASPICE-compliant development to meet functional safety and cybersecurity requirements;
- Cross-industry edge infrastructure know-how: Node-level architecture design across automotive, robotics, and manufacturing for scalable, low-latency, and fault-tolerant systems.
Have a question?
Speak to an expert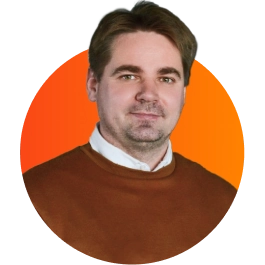