Mattias Andersson, CEO and Founder, MTEK
A McKinsey survey found that digital solutions are increasingly important in automation efforts. Nearly two-thirds (69%) of respondents already see them as a key part of their strategy, and an overwhelming majority (94%) believe they will be essential in the future. As a result, manufacturing software development services and digital transformation services are experiencing a surge in popularity. This surge in demand for digital automation tools aligns with projections of a growing industrial automation market. McKinsey estimates this market to reach a staggering $115B globally by 2025.
Fueled by this demand for digital solutions, manufacturing systems have transformed remarkably. The current era, Industry 4.0, is characterized by the rise of the Industrial Internet of Things and cloud-based solutions, enabling real-time data analysis for optimized production. Industry 5.0 envisions a future of autonomous manufacturing, where artificial intelligence and intelligent systems make data-driven decisions and drive production processes.
Manufacturing is transitioning from manual labor to automation, driven by robots and computer-controlled systems. Digital transformation aims to create intelligent, connected manufacturing systems to enhance efficiency, reduce waste, and promote sustainability.
The benefits of digital transformation in manufacturing include:
- Increased efficiency and productivity: Data-driven approaches incorporating automation, data analysis, and improved planning can streamline processes, minimize waste, and optimize production schedules. This leads to an increase in efficiency and productivity.
- Reduced costs: While there's a need for initial investment, digital transformation can lead to long-term cost savings. Savings can come from reduced waste, lower energy consumption, optimized inventory management, and improved labor efficiency.
- Improved decision-making: Data-driven insights from digital tools empower manufacturers to make informed decisions about production planning, resource allocation, and maintenance schedules.
- Greater agility and flexibility: With digital transformation, manufacturers can respond rapidly to customer demands and market changes. They can adjust production lines faster, personalize products, and respond more effectively to disruptions.
- Enhanced brand reputation: Consumers are increasingly demanding sustainable and ethically produced goods. By embracing digital transformation and prioritizing sustainability, manufacturers make their brands more attractive to environmentally conscious consumers.
Nonetheless, this digital transformation is accompanied by challenges, high initial investments, demand for skilled labor, and cybersecurity threats.
The challenges of digital transformation in manufacturing include:
- Cost and investment: Implementing technologies like AI, cloud computing, and IoT requires significant upfront investment. This can burden smaller businesses or those with limited financial resources.
- Data integration and management: Digital transformation generates vast amounts of data. Manufacturers need robust systems to integrate data from various sources (e.g., production lines, sensors, supply chain partners) and ensure accuracy and security.
- Skilled workforce: Data analytics, automation, and cybersecurity skills are necessary for operating and maintaining new digital technologies. Manufacturers may need to invest in training programs or recruit talent with these skill sets.
- Legacy systems: Many firms rely on outdated software and equipment that may not be compatible with new digital technologies. Upgrading or replacing these legacy systems can be time-consuming and costly.
- Security concerns: Digital transformation increases a manufacturer's vulnerability to cyberattacks. Protecting sensitive data and operational systems requires robust cybersecurity measures.
So, what technologies will mitigate the challenges and bring out the benefits of digital transformation in manufacturing?
Read more: 2023 guide to digitization in manufacturing in 5 essential steps
6 technological trends that will reinforce digitalization in manufacturing
The manufacturing industry thrives on innovation. As technology continues to evolve, so do the processes that drive production. We'll examine how these trends fundamentally transform how goods are produced, focusing on increased speed, accuracy, and adaptability.
1. Automation in manufacturing
The vast potential for automation in the manufacturing sector remains largely untapped. A McKinsey Global Institute study analyzing manufacturing work across 46 developed and developing countries (representing 80% of the global workforce) reveals this. Even though manufacturing is already a highly automated industry, significant automation opportunities exist within factories and related areas like supply chain and procurement. The study suggests data collection, processing, and predictive physical tasks hold the highest potential for automation advancements.
Modern factories, empowered by digital technologies, are undergoing a significant transformation—automation is at the heart of this change. Advances in data analysis, AI, and ML have reshaped manufacturing. These advancements and a growing pool of technology providers offer manufacturers various solutions and applications to automate and enhance their operations.
Successfully implementing these automation technologies can lead to substantial benefits across various sectors. Documented improvements include reductions in machine downtime (30-50%), increases in production throughput (10-30%), gains in labor productivity (15-30%), and enhanced forecasting accuracy (up to 85% improvement). These improvements directly translate to a more efficient and competitive manufacturing environment.
The benefits of automation for your business:
- Lower operating costs and labor savings;
- Improved worker safety;
- Faster ROI (Return of Investment);
- Ability to be more competitive;
- Production efficiency, quality, and consistency;
- Efficient use of floor space.
The challenges of implementing automation:
- High upfront costs and ongoing maintenance.
- Workforce disruption and skill gap
- Technical complexity and integration challenges.
Read more: Application of Artificial Intelligence in manufacturing
2. IoT and robotics in manufacturing
The ongoing digital transformation in manufacturing requires constant innovation and the increasing adoption of the latest technological advances for automation. One trend that allows manufacturing companies to speed up their processes is robotics engineering.
Currently, approximately 3.9M industrial robots are operating in factories worldwide. Notably, the automotive industry leads the pack with 30% of all robots, followed by electronics and electrical (26%) and the metal industry (11%). The International Federation of Robotics (IFR) predicts continued growth for the industrial robot market. In 2023 the market was expected to surge by 7%, reaching over 590,000 units shipped globally. This signifies a significant increase compared to the $15.8B value of new installations in 2022. Furthermore, the IFR forecasts a steady 7% annual growth for the market until 2026. The long-term growth trend for worldwide installations is expected to reach 718,000 units in 2026, showing no signs of slowing down.
Also, the IoT in manufacturing market size was valued at $50B in 2021 and is expected to reach $87.9B by the end of 2026, showing a CAGR of 11.9% from 2021 to 2026.
With IoT solutions and robotics, manufacturing sites can automate production lines and processes, closely monitor complex processes, analyze performance, and determine where improvements can be made.
Benefits of robotics in manufacturing:
- Improved quality and consistency. Robotics and other technologies, such as industrial IoT or 3D printing, allow manufacturing companies to provide better production quality. They also help reduce cycle times and introduce real-time monitoring to improve preventive maintenance. Manufacturers gain more control over their production processes by combining robotics, IIoT, 3D printing, and other advanced technologies. This leads to improved product quality, greater consistency, and, ultimately, higher customer satisfaction.
- Increased productivity. As a result of the speed and efficiency of robotic solutions, throughput can be maximized.
- Greater safety. Using robots for repetitive tasks reduces the risks of injury for workers, especially under hostile conditions.
- Real-time information. Sensors allow manufacturers to receive real-time information about the processes and machinery conditions.
Challenges of implementing robotics in manufacturing:
- High initial investment. The introduction of automated manufacturing systems requires a substantial upfront investment.
- Rare expertise. Robotics in manufacturing is a sophisticated system with complex operation, maintenance, and programming needs. Understanding the costs of personnel investment is essential.
- Ongoing costs. While robots may reduce some manufacturing labor costs, they have expenses, such as maintenance.
Keep reading: IoT trends that will rule in manufacturing
3. Predictive maintenance
As the number of sensors and other IoT devices grows, so does the amount of information about hardware, robots, and other machinery. Another way for manufacturers to reduce costs and optimize their processes is to invest in predictive maintenance. Manufacturing sites typically rely on reactive maintenance, often with huge expenses, extended downtime, and process disruption. On the contrary, predictive maintenance allows the manufacturing industry to reduce the upkeep cost by 25% to 30%. This shift towards predictive maintenance is a key aspect of digital transformation in manufacturing, enabling data-driven decision-making to optimize production processes and minimize disruptions. Also, it helps to reduce downtime and align maintenance schedules to create as little disruption as possible.
Why do companies need predictive maintenance?
Traditional maintenance approaches, whether reactive (fixing breakdowns) or proactive (relying on experience to anticipate issues), have limitations. Predictive maintenance powered by the IoT offers a more effective solution for manufacturers.
One key driver of this advancement is predictive AI. By analyzing robot performance data, AI can identify the future state of equipment, allowing for proactive maintenance and preventing costly downtime. In the automotive parts industry alone, unplanned downtime can cost a staggering $1.3M per hour, according to the Information Technology & Innovation Foundation. Predictive AI helps manufacturers avoid such significant losses, playing a crucial role in digital transformation in manufacturing by ensuring optimal equipment performance and minimizing disruptions. However, implementing and integrating these technologies effectively across complex manufacturing systems can be one of the challenges of digital transformation in manufacturing.
Machine learning plays a further role in optimizing performance. These algorithms can analyze data from multiple robots performing the same task, identifying opportunities for improvement. As machine learning algorithms gain access to more data, their performance improves. Essentially, these technologies work together to refine processes and maximize efficiency continuously.
The advantages of adopting predictive maintenance are clear. Manufacturers gain control over repair costs and scheduling, leading to reduced unplanned downtime and the ability to eliminate potential failure points before they occur. Additionally, predictive maintenance utilizes non-intrusive testing methods, minimizing disruptions to ongoing operations.
Benefits of predictive maintenance in manufacturing:
- Optimization of operational expenses;
- Material cost savings (25 to 30%);
- Maintenance is performed as needed;
- Reduction of the maximum amount of downtime.
Challenges of predictive maintenance in manufacturing:
- Specific technology needs to be purchased;
- A lot of time is needed to implement it correctly.
However, we cannot ignore other data applications in manufacturing. Let’s examine how proper data management can improve other areas of manufacturing.
4. Predictive analytics in manufacturing
Many manufacturing companies, especially in the further phases of their maturity, collect large amounts of data from many sources. If treated properly, this data opens up a whole new world for manufacturers. Digital transformation in manufacturing is a complex solution that combines Big Data, ML algorithms, and cloud computing software tools. It plays a crucial role in interpreting and predicting:
- Consumer demand;
- Employee productivity;
- Safety issues;
- Areas of improvement.
Take a look at the chart below to explore the areas of predictive analytics in manufacturing:
If appropriately used, predictive analytics is hugely beneficial for manufacturing:
- Allows to access sophisticated data-driven analytics, insights, and decisions;
- Improves forecasts and maximizes revenue;
- Helps bring the automation in manufacturing sites to the next level;
- Improves inventory management with demand forecasting;
- Enhances operational efficiency in real-time.
5. LEAN manufacturing
You may wonder what this trend has to do with technology. LEAN is a system or method focused on waste reduction. LEAN manufacturing focuses on the optimization of all processes and an overall reduction of waste of any type. Here are eight problems that LEAN manufacturing helps to solve:
LEAN is about smart resource use. It relies heavily on predictive analytics to make smart decisions and automation to better use available resources.
Short and long-term benefits of LEAN manufacturing:
- Improved quality. The smart approach to resource management allows manufacturers to focus on the quality of products;
- Increased efficiency. Balanced resources help companies to plan their work effectively;
- Easier to manage. Automation solutions and predictive analytics, key aspects of digital transformation in the manufacturing industry, make it easier to manage complex production sites.
- Safer work environment. Removing unnecessary elements from the operation helps manufacturers become more organized and creates an orderly and safe work environment.
- A bigger potential for the automation of manufacturing processes. When a company is focused on optimization and waste reduction, it is also eager to find ways to automate its manufacturing sites.
Depending on the planning and effort put into your implementation, you can still face some of the problems. Challenges you may face when implementing LEAN manufacturing:
- Resistance. The human factor can never be easy, as most people don't like change. Your long-term employees may struggle to convert to the new lean culture.
- Training. Many resources will be needed to help employees transition to a new framework.
- Upkeep. Like any process, LEAN manufacturing requires upkeep and maintenance.
6. ESG in manufacturing
Manufacturers are increasingly pressured to consider ESG (Environmental, Social, and Governance) factors throughout their supply chains. A key driver for this trend is consumer demand, particularly from millennials, who value sustainable practices. Companies are responding by looking for ways to reduce their carbon footprint, and digital transformation in manufacturing is playing a crucial role in achieving this goal.
Key areas of ESG-driven progress in manufacturing:
- Digital technologies like AI and cloud computing enhance manufacturing efficiency and reduce environmental impact through better data use, less waste, and lower energy consumption. However, one of the challenges of digital transformation in manufacturing is ensuring these technologies are implemented effectively and securely across a complex ecosystem.
- The need for transparency in the supply chain is growing as companies become more focused on ethical sourcing and sustainable practices.
- Designing products to last longer, be recycled or refurbished, and reduce waste through a circular economy is becoming more popular.
- ESG is driving innovation in manufacturing, with companies using new technologies to optimize resources and create eco-friendly products.
- Employee well-being and a positive work environment are key to attracting and retaining talent in a tight labor market.
- Manufacturers are increasingly aware of consumer demand for sustainable products and are designing and producing accordingly.
A MakeUK report reveals that 62% of manufacturers in the UK currently have ESG targets or KPIs in place.
Manufacturers are discovering substantial benefits when they weave Environmental, Social, and Governance (ESG) practices into their operations, according to Menzies:
- Cost savings and resource efficiency: ESG practices often lead to energy efficiencies, improving a company's ESG performance and generating cost savings. These savings can then be strategically reinvested in other areas of the business.
- Fueling innovation and opportunity: Strong ESG strategies are acting as catalysts for the emergence of new business opportunities. By prioritizing sustainability, manufacturers can position themselves at the forefront of innovative solutions that align with today's environmentally and socially conscious consumers.
- Enhanced cash flow and market competitiveness: Investments in research and development (R&D) driven by ESG considerations can yield significant financial rewards. These rewards can translate into improved cash flow and a more competitive edge in the marketplace.
- Building resilience for the future: By proactively embedding a well-defined ESG strategy, manufacturers are better equipped to capitalize on future competitive advantages. This proactive approach fosters long-term efficiencies that deliver continuous cost savings that can be reinvested in future endeavors, ensuring long-term sustainability for the organization.
While implementing ESG principles in manufacturing presents challenges, the potential benefits are significant. From cost savings and innovation to enhanced competitiveness and futureproofing, embracing ESG can deliver a strategic advantage for manufacturers. However, several key hurdles need to be addressed:
- Upfront investment: Implementing ESG initiatives often requires initial investments in new technologies, processes, and infrastructure.
- Supply chain complexity: Integrating ESG practices across a complex network of suppliers and partners can be challenging.
- Measuring impact: Quantifying the true environmental and social impact of ESG efforts can be difficult.
- Shifting corporate culture: Enacting lasting change often requires a shift in corporate culture, emphasizing long-term sustainability alongside traditional profit-driven goals.
Ultimately, strong ESG performance strengthens a company's reputation, brand image, and long-term profitability, positioning it for success in a world increasingly focused on sustainability and social responsibility.
Digital transformation in manufacturing: in-house vs outsourcing
Behind any digital transformation (in manufacturing or any other industry) is a team of people who make it happen. Most companies think about digital transformation in manufacturing only in terms of two dimensions: either having an in-house team or outsourcing. Let’s take a look at some pros and cons of both approaches.
In-house for digital transformation: pros and cons
Having an in-house team is better because of:
- Control. It’s easier to manage a team that sits next to you.
- Deeper understanding. When the team sees the processes they need to transform, it helps them to understand business values better.
- Talent development. If you need specific skills, you can develop them in your employees how you need them.
However, you should be ready for:
- Talent development costs. Yes, you can develop the talent you need within the company, but you will also pay for it.
- Great expenses. Finding a suitable team with relevant experience in your location can cost a fortune.
- Time. Hiring in-house personnel with the required expertise can take 6 to 12 months.
- Limited access to experts. In most cases, persuading an expert to relocate for a relatively short-term project is hard, so you will have to choose from the local tech talent pool.
Outsourcing digital transformation in manufacturing: pros and cons
Benefits of outsourcing include:
- Cost efficiency. No explanation is needed here.
- Access to a larger talent pool. Thus, you will be able to find the necessary expertise.
- Ability to scale the team. Whether you need to scale up or down, your vendor will handle that.
- No extra capital expenses. There’s no need to find a bigger office, equip new workplaces, etc. You just hire a dedicated team and can work with it regardless of their location.
However, you need to be ready to face some challenges:
- More complicated communication. Outsourcing teams may need more clarification and guidance. Plus, pay attention to the time zone differences.
- Harder to manage. It requires more time and attention. However, with a reliable vendor, you just need to appoint an in-house Product Owner or Project Manager or simply have a dedicated person your outsourced team can contact.
However, the BCG study shows that among the companies that successfully implemented or are actively digitalizing manufacturing sites, 92% are using a combination of in-house and outsourcing resources.
How can N-iX help you with digital transformation in manufacturing?
N-iX is a global software development company with 2,200 experts who have experience working with business cases of different shapes and sizes. We have office locations and delivery centers throughout Europe, North America, and Latin America. We see cooperation with our clients as a fusion of your ideas and our technical expertise.
N-iX has helped many companies in manufacturing and related industries with their digital transformation:
- Fluke Corporation is a US-based company that manufactures, distributes, and services electronic test tools and software for measuring and condition monitoring. We have helped the client to improve asset maintenance by arming maintenance teams with critical asset information in real-time and tools that can effectively process it.
- A leading automotive technology company (under NDA) engaged the N-iX team to participate in its digital transformation phase. The company had many manual processes that it targeted to transform through digitization. As part of their digital transformation, the client decided to digitize their car maintenance process and computerize the flow of warranty data between mechanics and vehicle manufacturers with a Cloud-based application.
- WEINMANN Emergency is a medical technology company that develops life-saving medical equipment for emergency medical services, hospitals, and the military. New products needed to be brought to market faster while complying with medical standards and regulations. N-iX has built a strong engineering team with deep expertise in embedded software development and experience delivering healthcare software products. Apart from expanding the product's functionality and releasing a new version of firmware that complies with the latest industry standards, the N-iX team has also implemented a predictive maintenance system that enabled cost savings, solution reliability, and seamless operation.
- Another client (under NDA) is a Global Fortune 100 multinational engineering and technology company from Germany. As a leading IoT company, our client offers innovative solutions for smart homes, smart cities, connected mobility, and manufacturing. It uses its expertise in sensor technology, software, and services, as well as its IoT cloud, to offer its customers connected, cross-domain solutions from a single source. They needed to redevelop the legacy platform; they did not have the comprehensive in-house expertise to address and solve multiple technical issues and make the platform efficient and scalable. N-iX is also working on a computer-vision solution based on industrial optic sensors, lenses, and Nivida Jetson devices that will allow this client to manage and track the goods non-touch.
- Metrima is an Automatic Meter Reading (AMR) manufacturer and supplier that provides solutions for collecting data on electricity, district heat, water, gas, and other types of energy. The company sought a dedicated development team to augment its in-house development forces.
Transform your manufacturing processes with AI: discover key use cases in the white paper
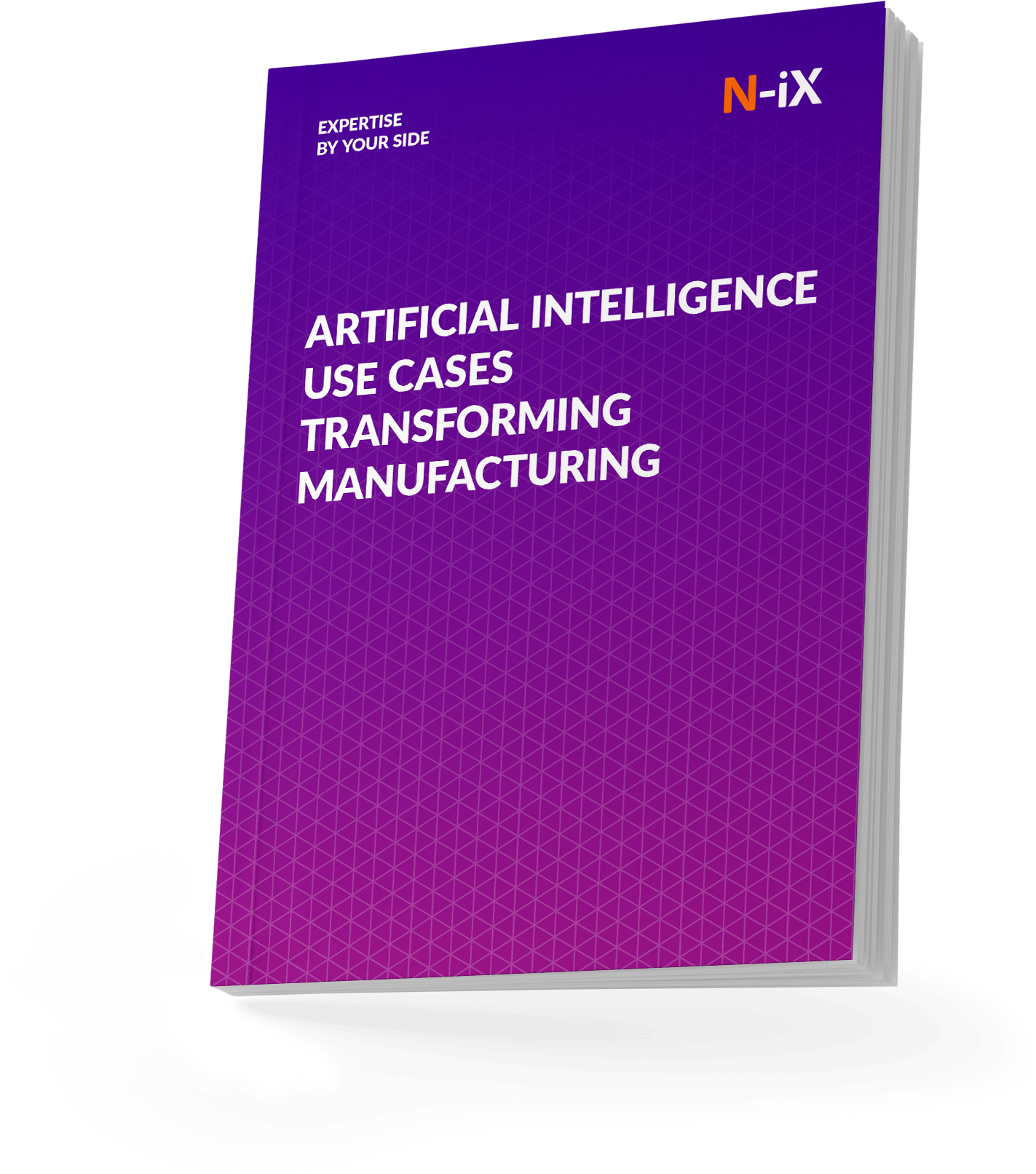
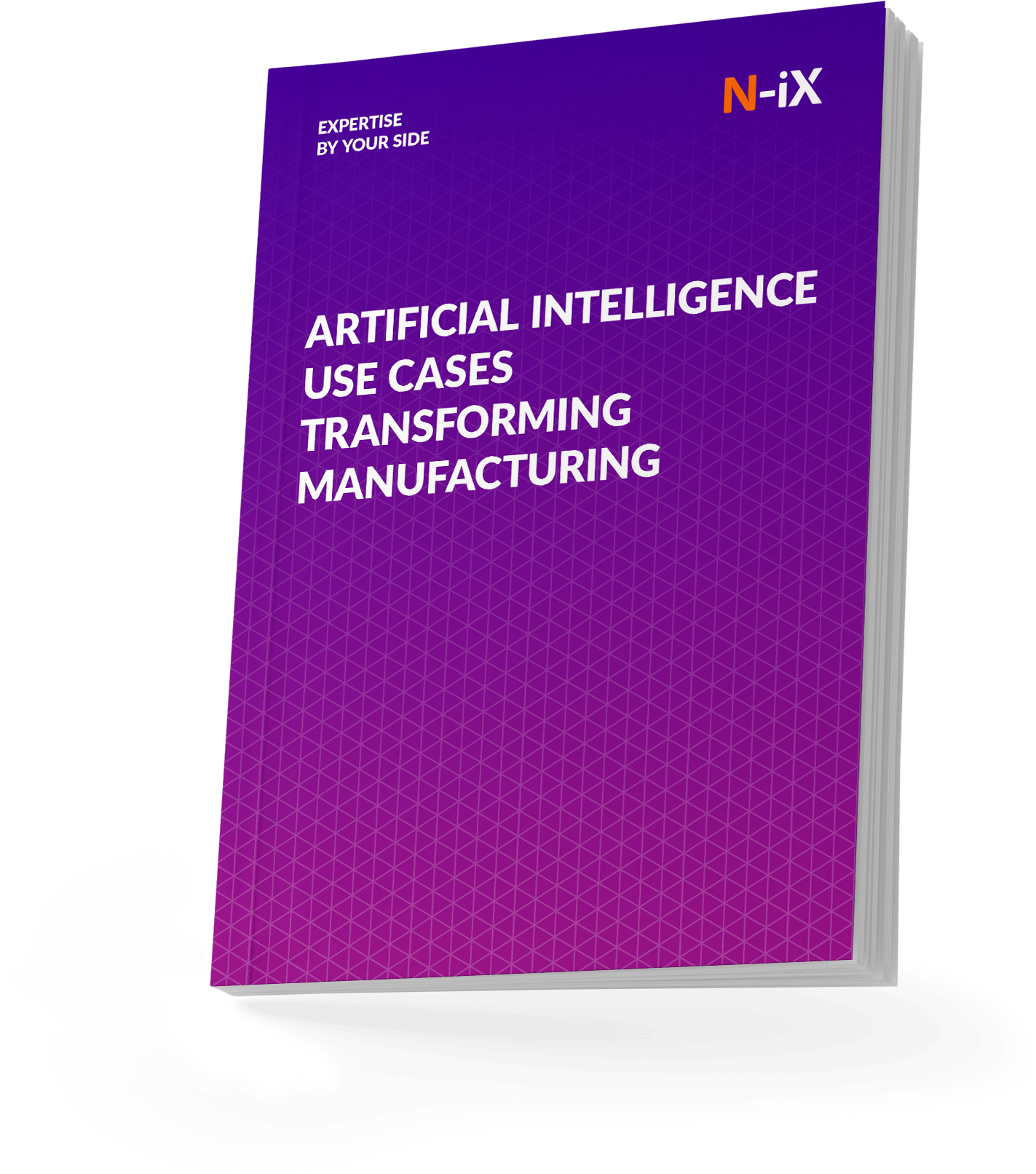
Success!
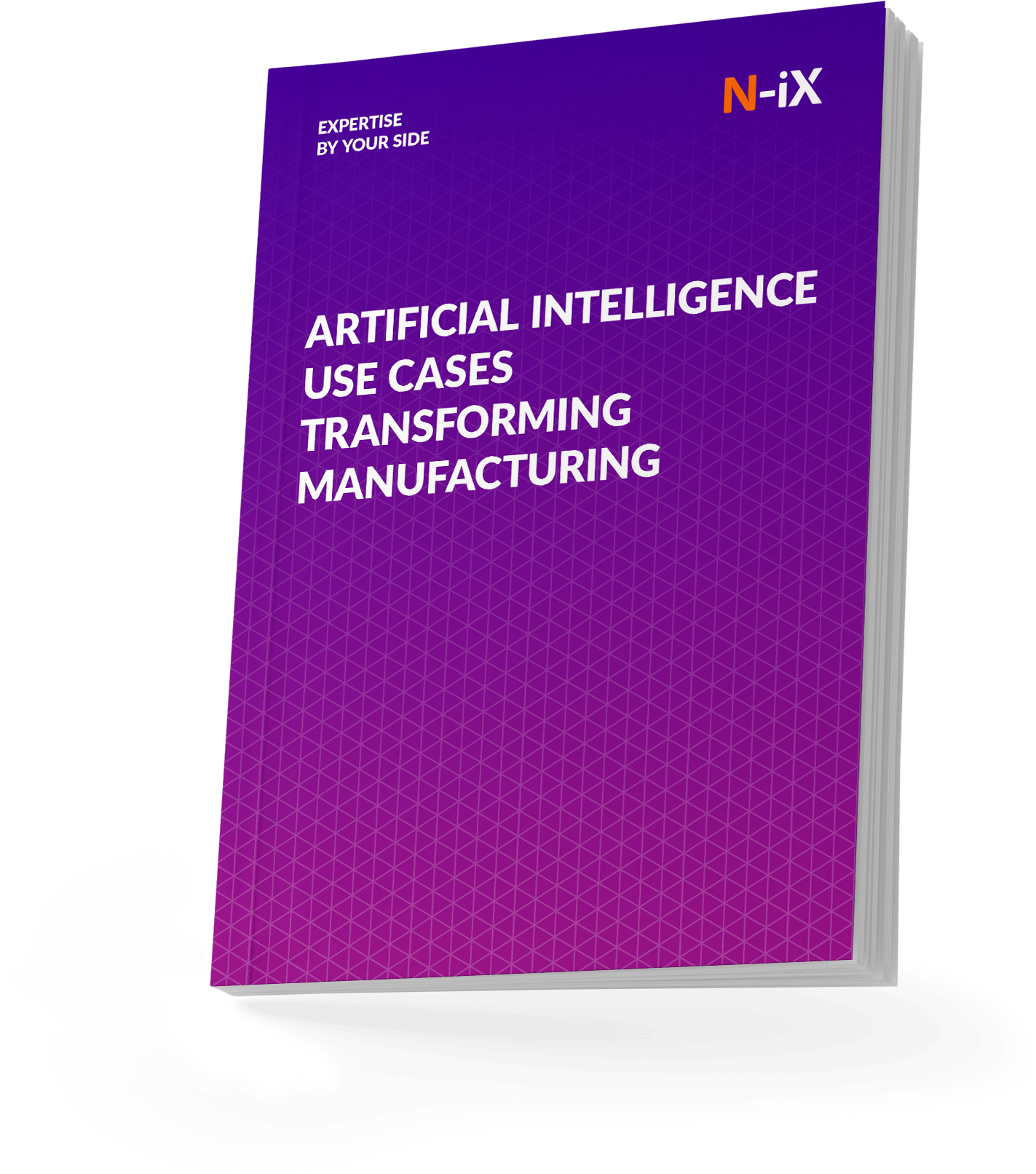
Have a question?
Speak to an expert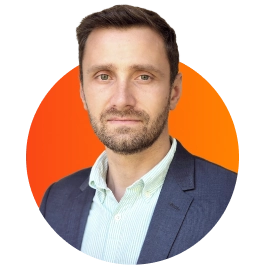