According to Transparency Market Research, the global robotics market will reach $147B by 2025. Yet, many enterprises struggle to fully capitalize on robotics technology advancements due to limitations, such as tasks requiring visual perception, of traditional robotic systems. Specifically, standard robotics systems often lack the sophisticated sensory capabilities necessary for complex, dynamic environments. Robots cannot adapt to variability without advanced sensory systems, leaving businesses with suboptimal performance.
Let's explore how integrating computer vision into robotics addresses these challenges.
How computer vision impacts robotics
Computer vision in robotics represents a convergence of visual perception and intelligent machine operation, enabling robots to "see" and interact with their environments in ways previously unattainable. This integration leverages advanced algorithms, deep learning, and sophisticated imaging technologies to provide robots with the ability to process and understand visual information.
To learn how computer vision transforms robotics, it's essential to understand the critical stages and technologies involved. Below, we delve into the key components and processes.
- The first step in any computer vision system is image acquisition, where robots capture images or video streams using various types of cameras, such as RGB cameras, infrared sensors, depth cameras, and stereo cameras.
- Once the images are captured, they undergo preprocessing to enhance quality and prepare them for analysis. This step may involve noise reduction, contrast enhancement, and normalization using techniques like histogram equalization.
- Feature extraction follows, identifying significant attributes from the preprocessed images. These features could include edges, corners, textures, or specific shapes.
- Object recognition is the next step. Computer vision enables the identification of specific objects within an image through Machine Learning models trained on large datasets to recognize patterns and features unique to different objects.
- Image segmentation then divides an image into multiple segments or regions, allowing robots to analyze and process each segment individually for more precise operations.
- Depth estimation determines the distance of objects from the camera, providing a sense of three-dimensional space required for tasks requiring spatial awareness, such as navigation and manipulation.
- 3D reconstruction creates a three-dimensional model of the environment or objects from 2D images. Applications like autonomous navigation require a detailed 3D map of the surroundings for path planning and obstacle avoidance.
- Motion analysis and tracking monitor and predict the movement of objects or people within the robot's field of view. This feature suits dynamic environments where robots must interact with moving objects or navigate changing scenes.
Industry use cases of computer vision in robotics
From streamlining logistics and manufacturing processes to advancing healthcare and agricultural practices, computer vision is changing various sectors by enhancing the functionality and efficiency of robotic systems. Let's define the diverse applications of computer vision in critical industries with real-world success stories by N-iX.
1. Logistics
Autonomous mobile robots (AMRs) with computer vision navigate complex warehouse environments autonomously. They use visual data to map their surroundings, avoid obstacles, and optimize their routes in real time.
Vision systems enable autonomous vehicles to navigate complex environments by detecting obstacles, recognizing traffic signs, and understanding road conditions. AMRs can handle repetitive and time-consuming tasks such as transporting goods, allowing human workers to focus on more complex and value-added activities.
Vision-guided robots can identify and locate items within a warehouse. These robots use computer vision to navigate aisles, recognize products, and pick orders efficiently. They also analyze package dimensions, labels, and barcodes to direct items to the correct destinations.
From our experience, N-iX has partnered with Redflex, an Australian-based company that develops intelligent transport solutions, to create a traffic management solution. The solution uses computer vision and deep learning to identify traffic violations, with impressive accuracy rates of approximately 88% for seat belt verification and 91% for distracted driving identification.
2. Manufacturing
Computer vision improves logistics by automating inventory management, sorting, and tracking. Vision systems can identify and count items, track their locations, and optimize storage arrangements. This automation enhances inventory accuracy, streamlines order fulfillment processes and reduces labor costs associated with manual inventory management.
In the manufacturing industry, N-iX helped a Global Fortune 100 conglomerate in the engineering sector enhance its inventory management system for more warehouses. The core component of this project was the Computer vision solution for docks, which allows contactless tracking of goods with industrial optic sensors and Nvidia Jetson devices. The solution integrated a computer vision system for automated goods tracking, which minimized manual work and optimized warehouse operations.
Computer vision in robotics can monitor the condition of machinery and equipment, detecting early signs of wear and tear. For example, cameras can detect oil leaks or overheating parts in industrial machines, triggering alerts for supervision teams to address problems before they escalate.
Keep reading: Applying robotics in manufacturing: technology requirements and use cases
Revolutionize manufacturing with Computer Vision – explore the guide now!
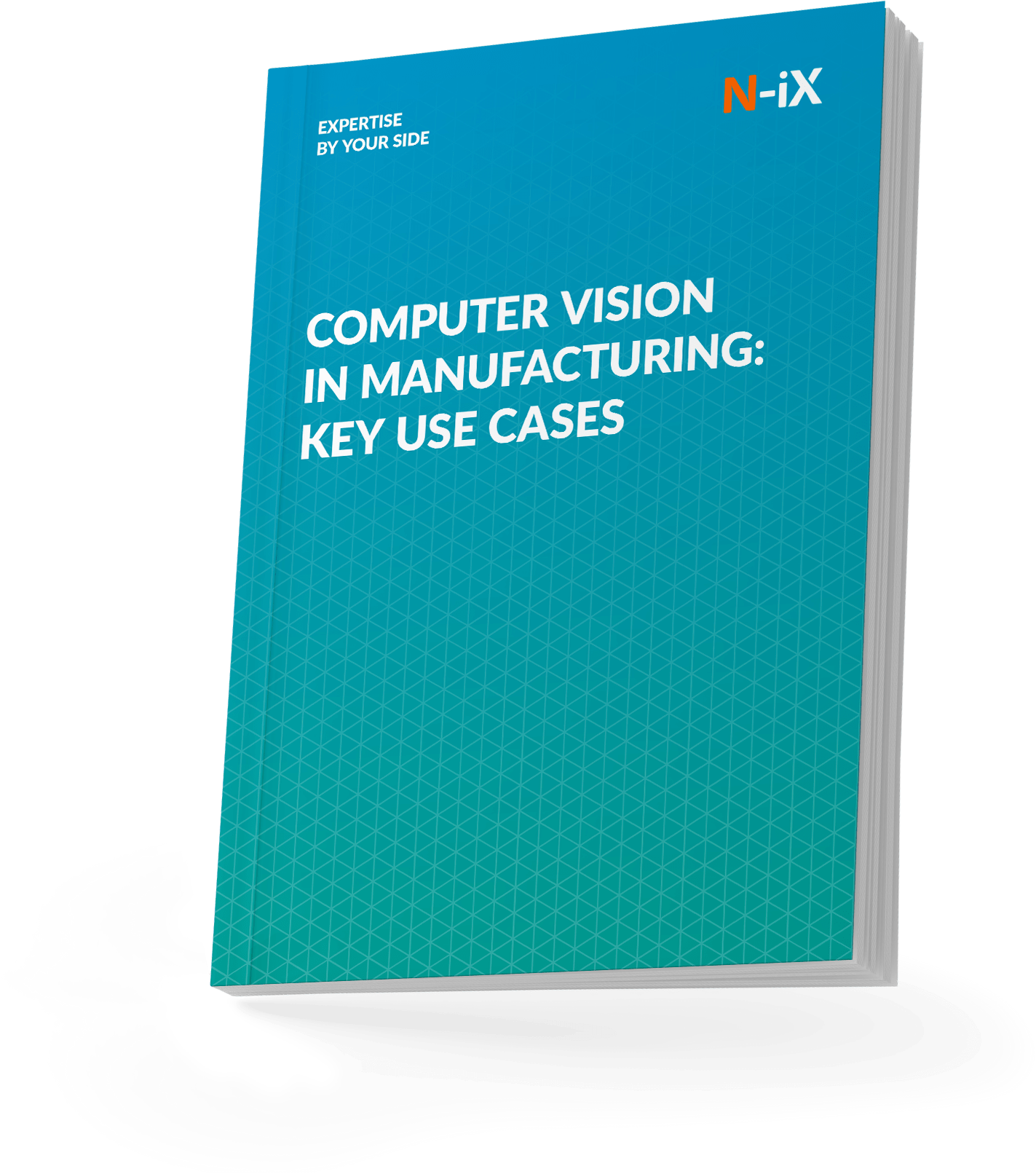
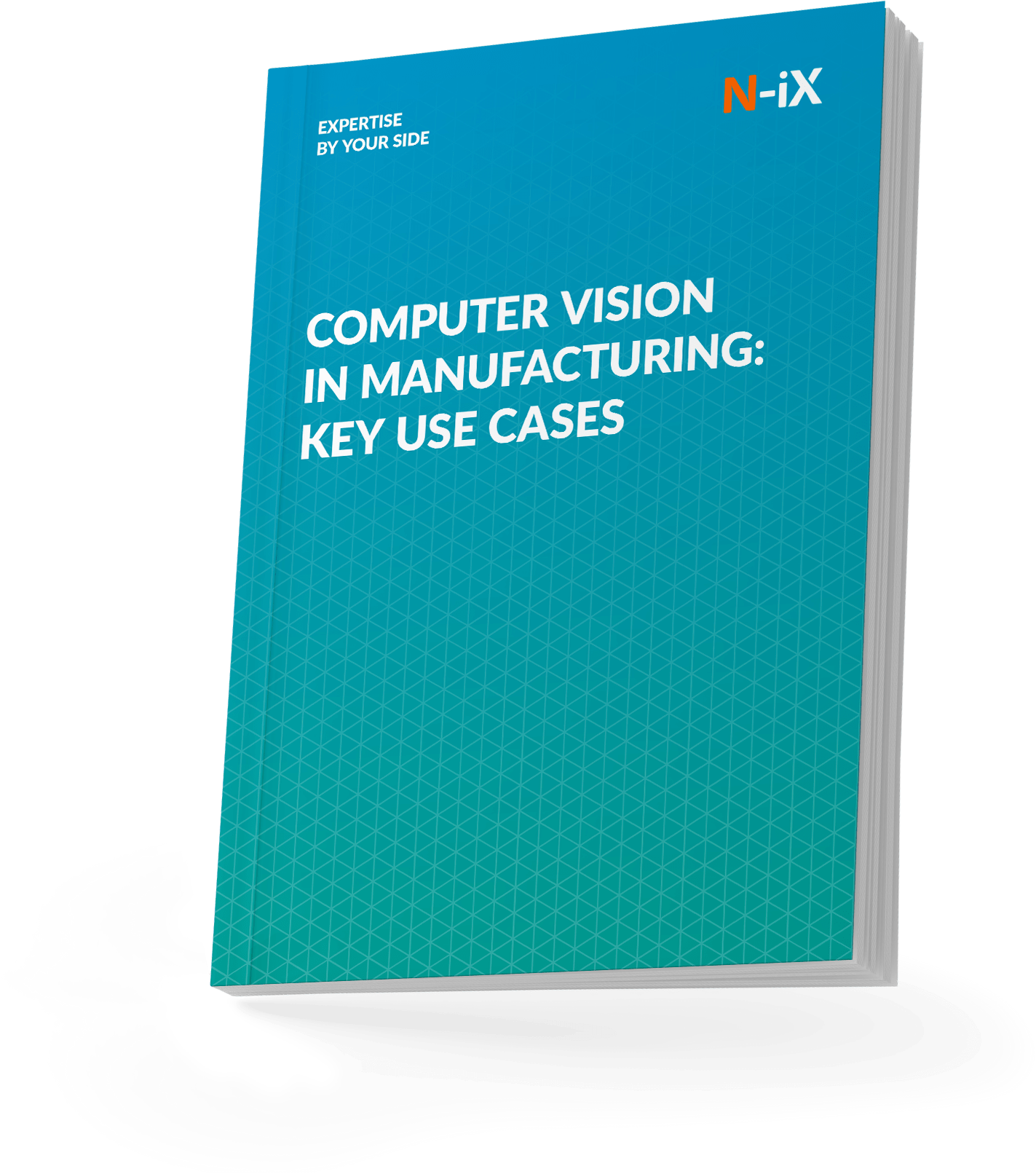
Success!
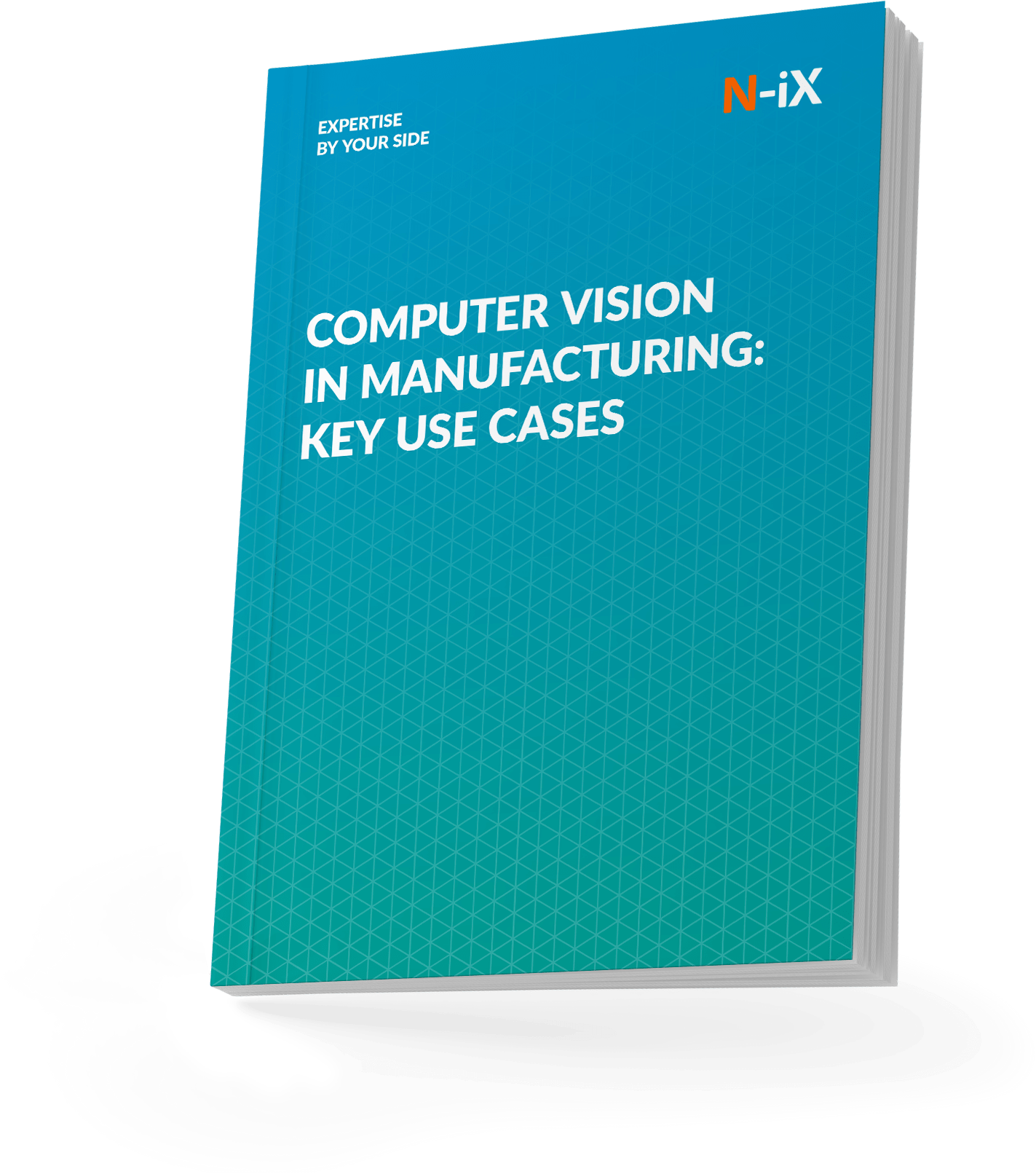
3. Healthcare
In healthcare, computer vision is important for image analysis and diagnosis. Progressive imaging procedures such as Magnetic Resonance Imaging and Computed Tomography scans generate complex visual data that computer vision algorithms can analyze to detect abnormalities and assist in diagnosis. For example, deep learning models are used to identify tumors, fractures, or other pathological conditions with high accuracy from medical images, providing valuable support to radiologists and clinicians.
Vision-based systems enable robots to assist with daily mobility, medication administration, and rehabilitation exercises. Robotic rehabilitation devices use computer vision to
- track patient movements and assess their progress,
- observe patients' vital signs,
- detect falls or unusual behavior,
- alert healthcare providers to potential issues.
Surgical robots equipped with computer vision provide surgeons with enhanced surgical field visualization. These systems enable precise control over surgical instruments, facilitating minimally invasive procedures. The da Vinci Surgical System uses computer vision to guide surgeons in performing complex surgeries with greater accuracy and less risk, leading to shorter patient recovery times.
Read more: Computer vision in healthcare: trends, use cases, and reasons to adopt
4. Retail
Computer vision in robotics significantly automates stock tracking and verification processes. Vision systems with cameras and image recognition algorithms can monitor warehouse shelves and storage areas, identify inventory levels, and detect out-of-stock conditions.
For instance, automated inventory systems use computer vision to scan barcodes or QR codes, update stock levels in real time, and generate alerts for restocking. Enterprises can reduce the reliance on manual checks, minimize stock discrepancies, and improve the accuracy of inventory data.
Vision-guided robots identify and select the correct items from shelves. These robots use advanced image recognition algorithms to locate products, even in cluttered environments, providing accurate order fulfillment. For example, companies like Amazon employ vision-guided robots to automate the picking process, significantly reducing the time needed to process orders and improving overall warehouse productivity.
5. Agriculture
Crop monitoring systems use computer vision to analyze aerial images drones or satellites capture. These systems can detect signs of disease, pest infestations, and nutrient deficiencies early, enabling timely interventions. Drones equipped with vision technology can survey large fields and identify areas infested with pests. Furthermore, ground-based robots with computer vision can patrol fields, identifying and eliminating pests on sight.
Harvesting automation is another area where computer vision is making significant strides. Robotic harvesters equipped with vision systems can identify ripe fruits and vegetables, picking them with precision and care. For example, robotic strawberry pickers use computer vision to locate and harvest ripe strawberries, ensuring only the best quality fruits are selected.
Computer vision in robotics greatly benefits precision agriculture in creating detailed insights into crop health, yield estimation, and automated harvesting. Advanced imaging techniques, such as multispectral and hyperspectral imaging, enable farmers to monitor the health of their crops with unprecedented accuracy. These systems can detect nutrient deficiencies, water stress, and disease symptoms early, allowing for timely interventions.
Overcoming challenges when implementing computer vision into robotics
Implementing computer vision in robotics presents unique challenges that require tailored solutions. Here are some specific hurdles and how N-iX addresses them.
Data quality and annotation
Ensuring high-quality data for training and validating models is a primary challenge in computer vision for robotics. Data quality issues often arise from noisy, incomplete, or unrepresentative datasets, which can significantly impact the performance of computer vision systems. Additionally, accurate data annotation-such as labeling objects, defining bounding boxes, and categorizing image content-is crucial for practical model training.
N-iX approach: We employ rigorous data collection and annotation processes to produce high-quality datasets. Our practice uses automated annotation tools and human verification to maintain accuracy and consistency.
Variable lighting conditions
Robotic systems often operate in environments where lighting conditions can vary significantly. These variations can affect the accuracy of computer vision systems, leading to potential errors in object detection and recognition.
N-iX approach: We develop robust algorithms that adapt to different lighting conditions. Our team uses advanced image preprocessing techniques, such as histogram equalization and adaptive thresholding, to normalize lighting variations.
Occlusion and object overlapping
In dynamic environments, objects may be partially or fully occluded by other objects, making it difficult for computer vision systems to detect and recognize them accurately. It can be a significant obstacle in applications like warehouse automation and autonomous navigation.
N-iX approach: Our approach uses advanced deep learning techniques such as Region Proposal Networks (RPNs) and multi-view imaging to overcome occlusion. By integrating multiple camera angles and perspectives, we guarantee that objects can be identified even when partially hidden.
Computational resource constraints
Robotic systems often have limited computational resources, challenging to run complex computer vision algorithms. This is particularly true for mobile robots that need to be lightweight and power-efficient.
N-iX approach: We optimize computational efficiency by implementing lightweight neural networks and deploying models on specialized hardware such as GPUs and TPUs. We also use techniques like pruning and quantization to reduce model size and improve inference speed.
Hardware and software Integration
Integrating computer vision with robotic systems is a multifaceted challenge that involves aligning hardware components, such as cameras and sensors, with software frameworks. Ensuring compatibility between vision systems and robotic controllers is essential for smooth operation.
N-iX approach: Our process includes thorough compatibility testing and custom API development to bridge gaps between disparate systems for robust and reliable operation.
Botttom line
From manufacturing lines humming with efficiency to healthcare systems performing precise diagnostics and surgeries, the impact of computer vision is profound and far-reaching. Imagine robots that can see and interpret their surroundings with human-like precision, making real-time decisions that drive productivity and innovation. This is the future that computer vision promises and is already delivering.
Overcoming the challenges of integrating computer vision into robotics-such as handling real-time processing, guaranteeing data quality, and managing complex environments-is no small feat. But with N-iX's expertise, these challenges become opportunities for innovation and growth. We leverage cutting-edge technologies, optimize computational processes, and ensure seamless integration to help businesses unlock the full potential of their robotic systems.
Contact us to learn how we can tailor our computer vision solutions to redefine your operations.
Why talk to N-iX about computer vision integration with robotics?
- With over 22 years of market experience, N-iX has successfully delivered projects across various industries.
- The average client engagement at N-iX lasts between 3-10 years, reflecting the long-term value and trust that clients place in our services.
- N-iX has a team of over 200 data, AI, and ML experts, as well as over 2,400 software engineers and IT experts.
- N-iX is recognized as a rising star in data engineering by ISG, demonstrating the company's expertise and reputation in the industry.
- N-iX has a diverse technological experience, including Big Data, ML, Cloud, IoT, embedded software, VR, etc.
Have a question?
Speak to an expert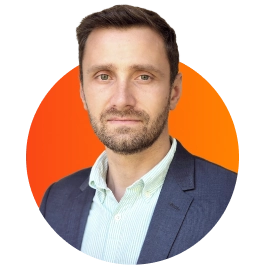