Whether you are just embarking on a journey of implementing an automated testing system for automotive relays, looking for ways to address existing testing's shortcomings, or generally interested in enhancing efficiency and reliability through automation—keep reading. We want to share our experience deploying an automated relay testing solution specifically designed for the automotive sector. The automation of testing in relay-based systems can significantly improve efficiency and reliability and address the limitations inherent in manual testing methods.
What is a relay, and how does it work?
A relay is a simple control system component. It allows for switching power units in a device upon a command from a microcontroller. Relays vary. They switch loads of different powers, from a few watts to kilowatts.
In principle, they have an electromagnetic coil that attracts a contact group when activated and releases this group when the coil's power is cut off.
The general diagram of the relay and its detailed appearance are shown below.
It works very simply. You apply a control voltage to the coil's terminals. A magnetic field is created, pulling the movable contact towards the stationary one and closing them. When activated, two other terminals switch the load.
In spite of their critical function, relays are vulnerable to failures caused by unsuitable electrical or environmental conditions.
Why can relays fail?
Relays work well when used correctly. If used in the wrong conditions, they can fail. The main reasons for failure are not meeting electrical and environmental needs, such as:
- Correct voltage and power use;
- Maximum current/voltage and life span;
- Quick response time;
- Preventing leaks and handling high current safely;
- Working in the right temperature and humidity;
- Withstanding bumps and dirt.
Remember, the specs in the manuals are averages. Each batch of relays might vary a bit. So, real performance is best checked through tests on samples from each batch.
Detecting problems and testing automotive relays before implementation
Prior to implementation, relay testing is crucial for identifying issues, utilizing three main procedures: Setup, Control, and Testing, detailed in the table below, aimed at ensuring their reliability and efficiency.
N-iX testing solutions
We encountered the need for relay testing while developing a relay switch between two automotive ECUs (Electrical Computing Units). It was supposed to switch 50 contacts following a specific timing protocol. Unfortunately, one of the relays malfunctioned inconsistently, and it took us over a month to identify the fault. Since then, we have implemented hardware-in-the-loop (HIL) testing procedures for relays, even those from verified brands. Sometimes, a relay may have up to 1,000,000 on-off cycles with periods reaching 5 and 10 milliseconds, respectively. It can operate at high power, making the testing procedure complex. Therefore, we automated it. We developed a solution consisting of two key components: a test stand and an application running on a computer (as shown in a visual below). The stand allows flexible configuration of the load, voltage, and temperature during the test. It can turn the relay on and off at various frequencies, setting the most incredible test trajectories. Meanwhile, the application lets you build these trajectories, set test requirements, and generate a report. We built it using a Model-based approach with Simulink and Matlab, allowing us to automatically conduct any test from Table. We would be delighted to demonstrate how it works in person.
Conclusion
Automating relay testing allows for efficient detection and resolution of faults, significantly reducing the time and resources required for this process. Our solution, comprising a test stand and specialized software, ensures flexible and precise relay testing using a Model-based approach with Simulink and Matlab, enhancing the reliability and efficiency of automotive systems.
Launch a flawless product with IoT test automation! Discover how in the guide.
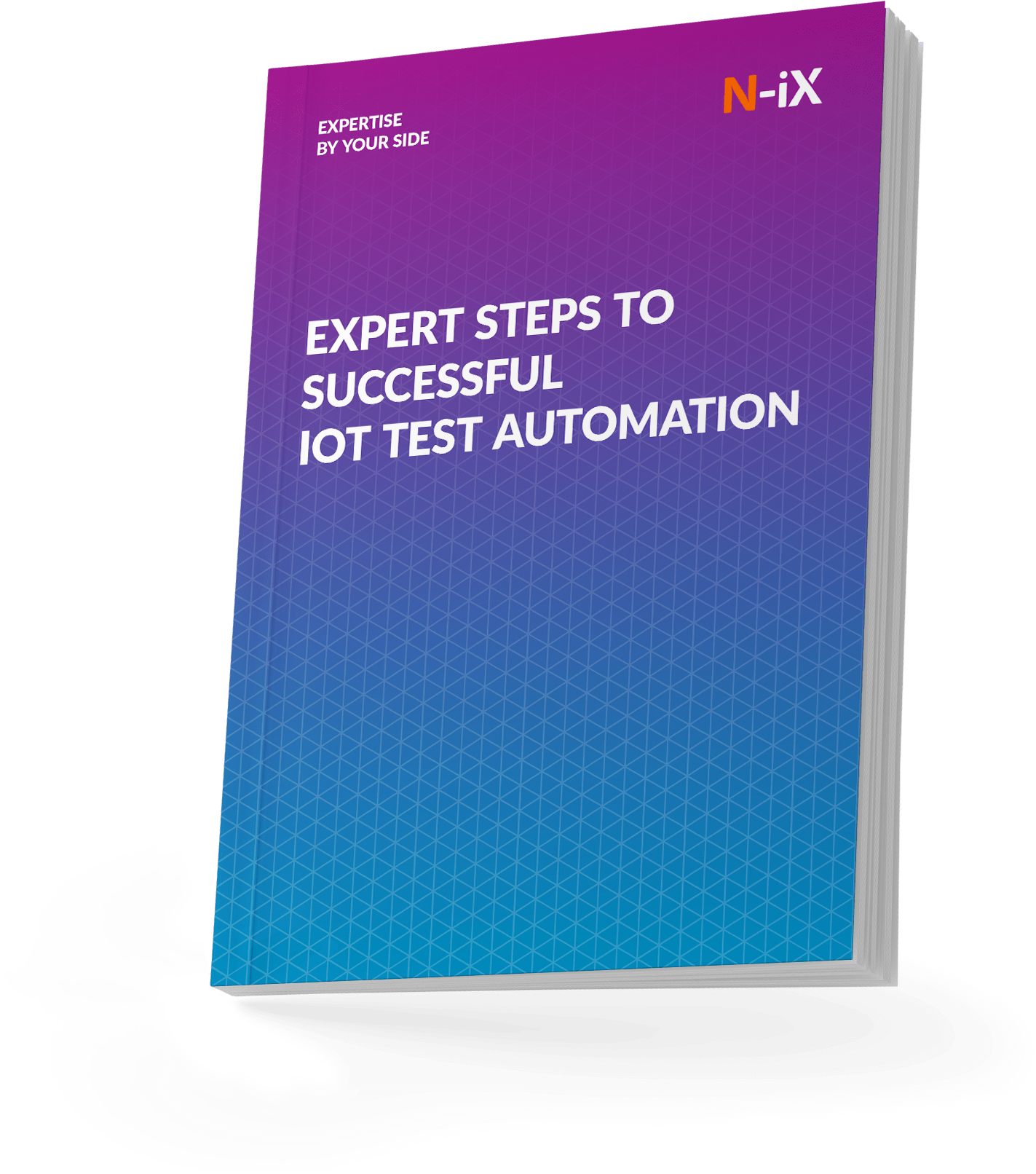
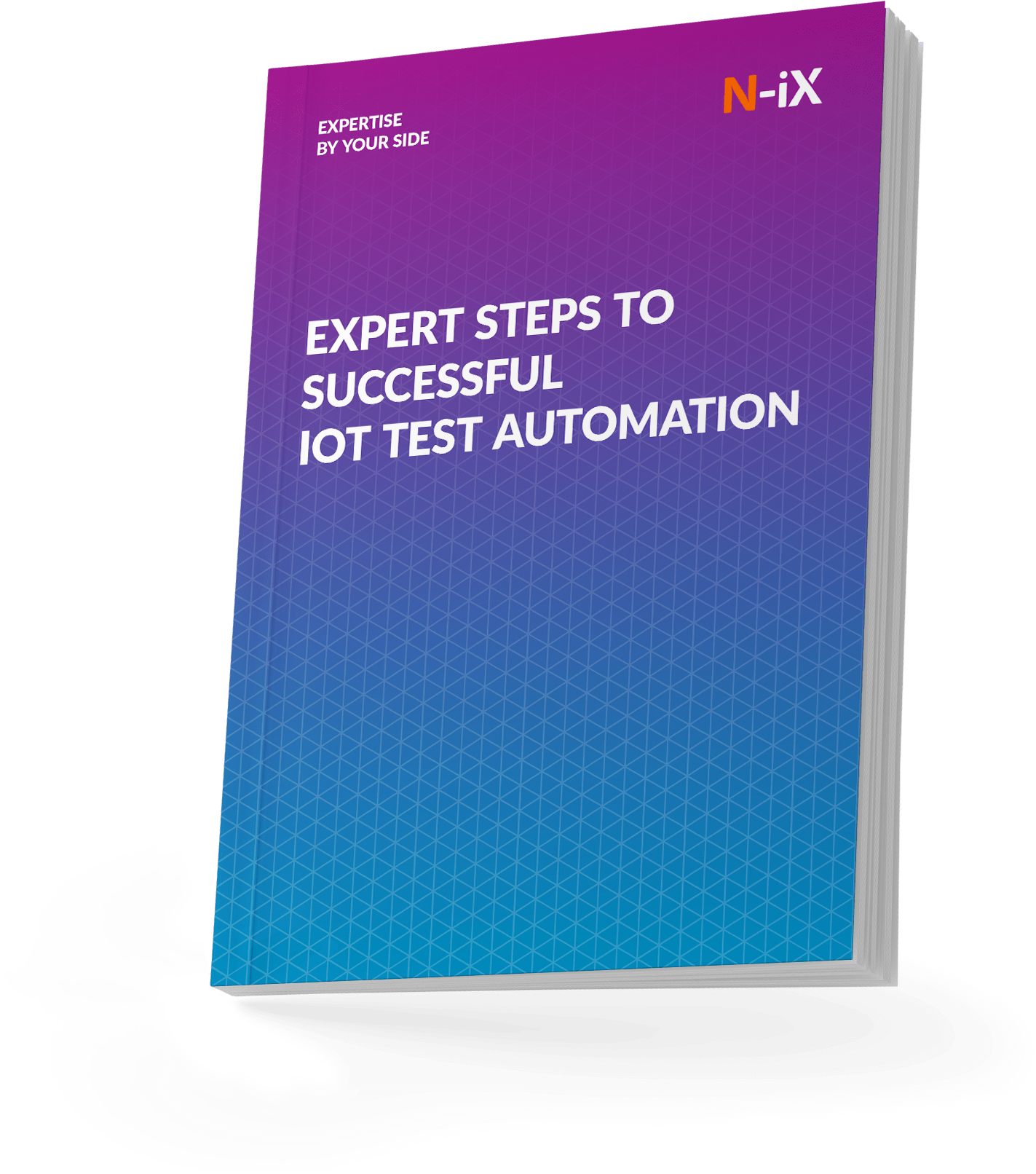
Success!
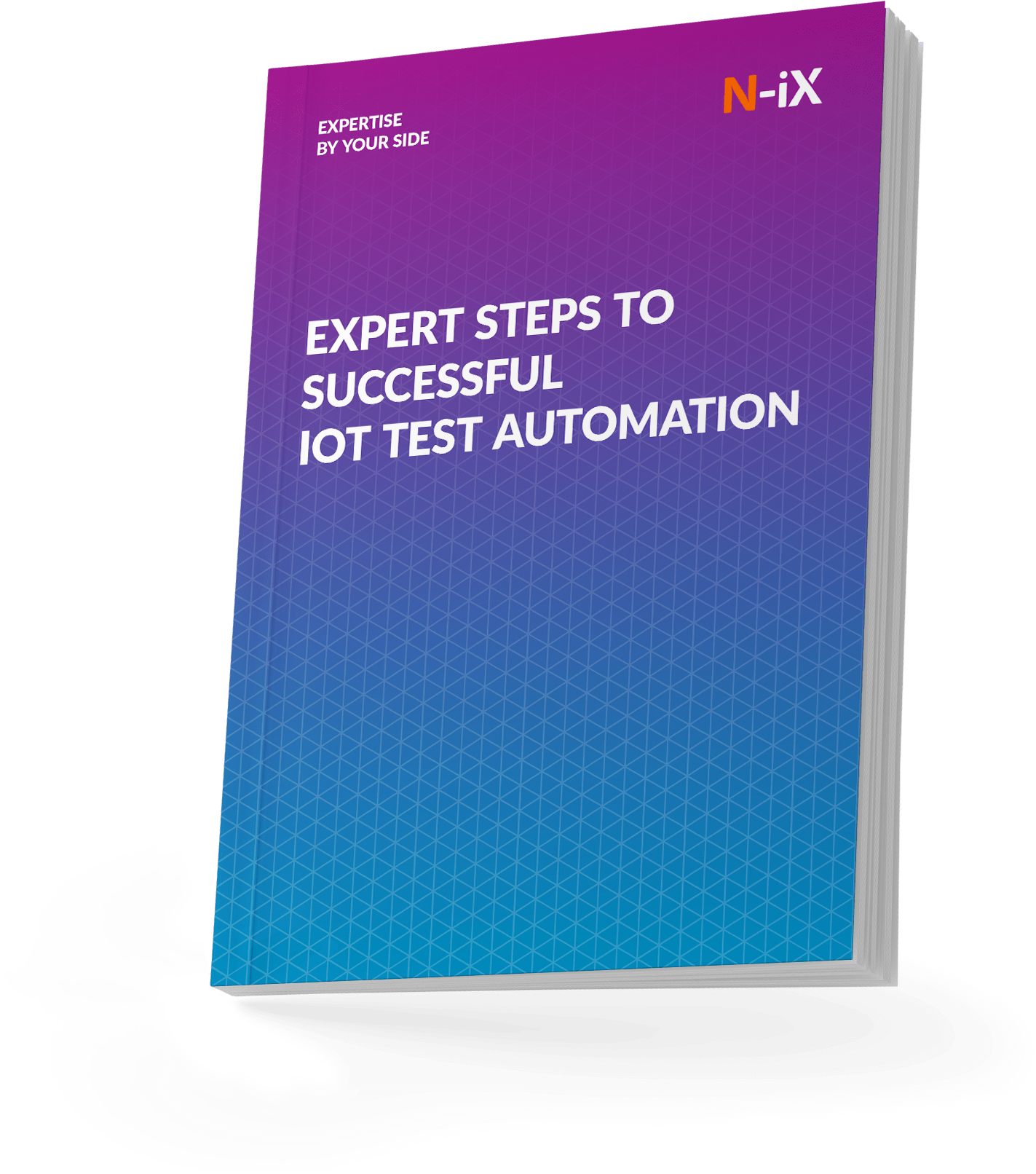
Have a question?
Speak to an expert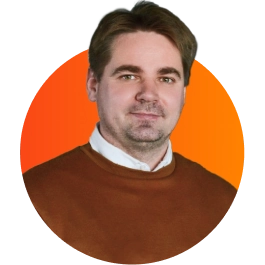