According to Deloitte, the manufacturing industry generates approximately 1,812 petabytes (PB) of data annually. Leveraging this data, Artificial Intelligence in manufacturing optimizes various processes by enabling advanced solutions, such as quality control improvement with Computer Vision or equipment uptime increase due to predictive maintenance.
The list of the use cases of AI in manufacturing software is extensive. Still, it is essential to choose the right solution to maximize the benefits of applying the technology. Below are the most impactful AI applications that help manufacturers enhance efficiency, reduce costs, and achieve operational excellence.
Use cases of Artificial Intelligence in manufacturing
AI powers various manufacturing processes, improving efficiency, reducing costs, and enhancing decision-making. Its impact grows when combined with AI-enabled technologies like Machine Learning, Computer Vision, and Generative AI. These technologies optimize workflows, enhance quality control, and enable rapid prototyping. Below are the most impactful AI applications in manufacturing.
Predictive maintenance
One of the AI applications in manufacturing makes it possible to predict when equipment or machinery will likely fail. Predictive maintenance solutions analyze historical data, sensor readings, and other factors to forecast potential issues before they occur, allowing for timely maintenance to prevent breakdowns.
This proactive approach is one of the most popular applications of Artificial Intelligence in manufacturing because of its benefits:
- Reduced downtime: Anticipating potential equipment failures allows for scheduled maintenance, reducing unexpected downtime that can disrupt production.
- Cost savings: Avoiding unplanned downtime and reducing the likelihood of major equipment breakdowns allows for saving costs associated with emergency repairs and replacement of machinery.
- Optimized maintenance schedules: With a more efficient allocation of maintenance resources, you can focus on equipment that needs attention rather than follow fixed schedules for all machinery.
- Extended equipment lifespan: Timely maintenance based on predictive analytics can prolong the machinery and equipment's life, ensuring they operate optimally for longer periods.
- Improved safety: Equipment in good working condition enhances workplace safety because there is less risk of accidents due to malfunctioning machinery.
Automation
AI-powered automation systems optimize manufacturing operations through real-time data integration and automated adjustments that reduce manual intervention. Intelligent production control systems use sensor data from equipment like CNC machines and injection molding systems to detect deviations in temperature, pressure, or vibration levels. When anomalies are identified, these systems automatically fine-tune machine parameters to maintain stable performance and prevent defects.
Automation also ensures smooth transitions between production stages. AI-powered systems dynamically reschedule equipment operations based on production priorities and reallocate tasks between workstations to prevent bottlenecks if one unit experiences delays.
These systems improve throughput, reduce idle time, and ensure consistent output quality. Manufacturers gain greater operational agility, allowing them to respond quickly to demand fluctuations and maintain production efficiency.
Warehouse and supply chain management
AI algorithms harness historical sales data, stock status, and market trends for accurate demand prediction. This optimization enables warehouses to manage inventory efficiently, reducing costs without compromising product availability.
Additionally, solutions that use Artificial Intelligence for manufacturing elevate warehouse order fulfillment. They analyze incoming orders, optimize picking routes, and allocate resources effectively, ensuring faster processing, fewer mistakes, and heightened customer satisfaction.
Quality control and production monitoring
AI-powered Computer Vision solutions enable manufacturers to automate quality control, monitor production lines, and optimize production processes. Visual inspection systems equipped with Machine Learning algorithms analyze camera images to detect defects, ensure component alignment, and verify product quality in real time. These systems continuously improve their detection accuracy and reduce false positives by learning from production data.
Beyond quality control, Computer Vision supports production monitoring by identifying bottlenecks, tracking production progress, and ensuring operational consistency. Automating these processes increases production speed and precision while reducing human errors and operational costs.
Integrating Computer Vision into manufacturing allows production lines to adapt quickly to changing demands, maintain product quality, and improve overall operational efficiency.
Collaborative robots
AI-powered collaborative robots (cobots) enhance manufacturing efficiency and safety by adapting to real-time conditions. Unlike traditional robots that follow static programming, cobots use Machine Learning and Computer Vision to recognize objects, adjust movements, and collaborate safely with human workers.
Cobots integrate AI-powered systems, including Computer Vision and motion control algorithms, to adjust their actions based on the environment and operator behavior. They assist in assembly, packaging, and quality control, reducing physical strain on workers and improving production speed.
The adoption of robotics in manufacturing enhances productivity, increases worker safety, and maintains production flexibility, especially in environments requiring frequent task adjustments. While cobots enhance human capabilities, broader AI-powered automation systems orchestrate machines and production flows independently to minimize manual intervention.
Digital twins
AI-driven digital twins replicate and predict manufacturing operations by processing real-time sensor data and historical performance metrics. ML models analyze system behavior, detect inefficiencies, and simulate process optimizations before making physical changes.
Manufacturers use digital twins to monitor production efficiency, simulate operational adjustments, and optimize production workflows without interrupting live processes. For example, a production manager can test whether increasing conveyor speed will improve output or cause errors before applying the change to the production line.
Digital twins also enhance production planning by identifying bottlenecks, testing alternative layouts, and validating product designs before manufacturing begins. They improve operational visibility, enable data-driven decisions, and reduce the risks and costs associated with trial-and-error adjustments on the factory floor.
Generative design
Generative AI is the core of generative design systems, which are used to develop complex shapes of products and blueprints to create them. The algorithm considers such parameters as materials, size, weight, and manufacturing methods to create lightweight and efficient structures.
Design engineers leverage this method in manufacturing to produce multiple design options for new products. This approach accelerates product development, especially when combined with additional manufacturing methods, like 3D printing. Its strength lies in fashioning intricate shapes that are lighter and sturdier than those created by conventional design methods.
The use of generative design in manufacturing results in budget savings due to the speed of development and economy of the materials.
Read more: Artificial intelligence outsourcing: How to get it right and boost your next project
Implementing AI in manufacturing: Success stories by N-iX
While the potential of Artificial Intelligence in manufacturing is widely discussed, its true value emerges when applied to solve complex operational challenges. N-iX helps leading enterprises apply AI, ML, and Computer Vision to enhance quality control, streamline supply chains, and optimize repair operations. The following case studies show how we help our clients reduce costs, improve efficiency, and strengthen operational resilience with AI solutions for manufacturing.
Hardware repair optimization with computer vision
A global provider of technology repair and maintenance services faced operational inefficiencies in its hardware repair processes. Manual inspection methods caused delays in service delivery, increased labor costs, and led to quality inconsistencies, limiting the company’s ability to scale efficiently.
To overcome these issues, N-iX developed and implemented an AI-powered Computer Vision system. The solution automated hardware diagnostics and defect detection, reducing reliance on manual inspections and enabling faster, more accurate assessments.
The system reduced the average troubleshooting time for laptop motherboards from 30 minutes to under 10 minutes. It lowered labor expenses, minimized errors, and improved overall repair process efficiency. Real-time tracking enhanced operational visibility, enabling the client to optimize workflows and increase customer satisfaction.
Supply chain optimization with Machine Learning
A German multinational engineering and technology company faced inefficiencies in its logistics operations. Manual shipment grouping, order processing, and delivery planning caused delays and increased operational costs.
N-iX developed a Machine Learning-powered solution to automate shipment grouping and streamline order processing. The system minimized manual input, accelerated delivery preparation, and improved planning speed.
The solution reduced logistics planning time, accelerated order processing, and improved delivery preparation efficiency. As a result, the company lowered operational costs and increased supply chain performance.
Build a future-proof AI strategy—get your guide now!
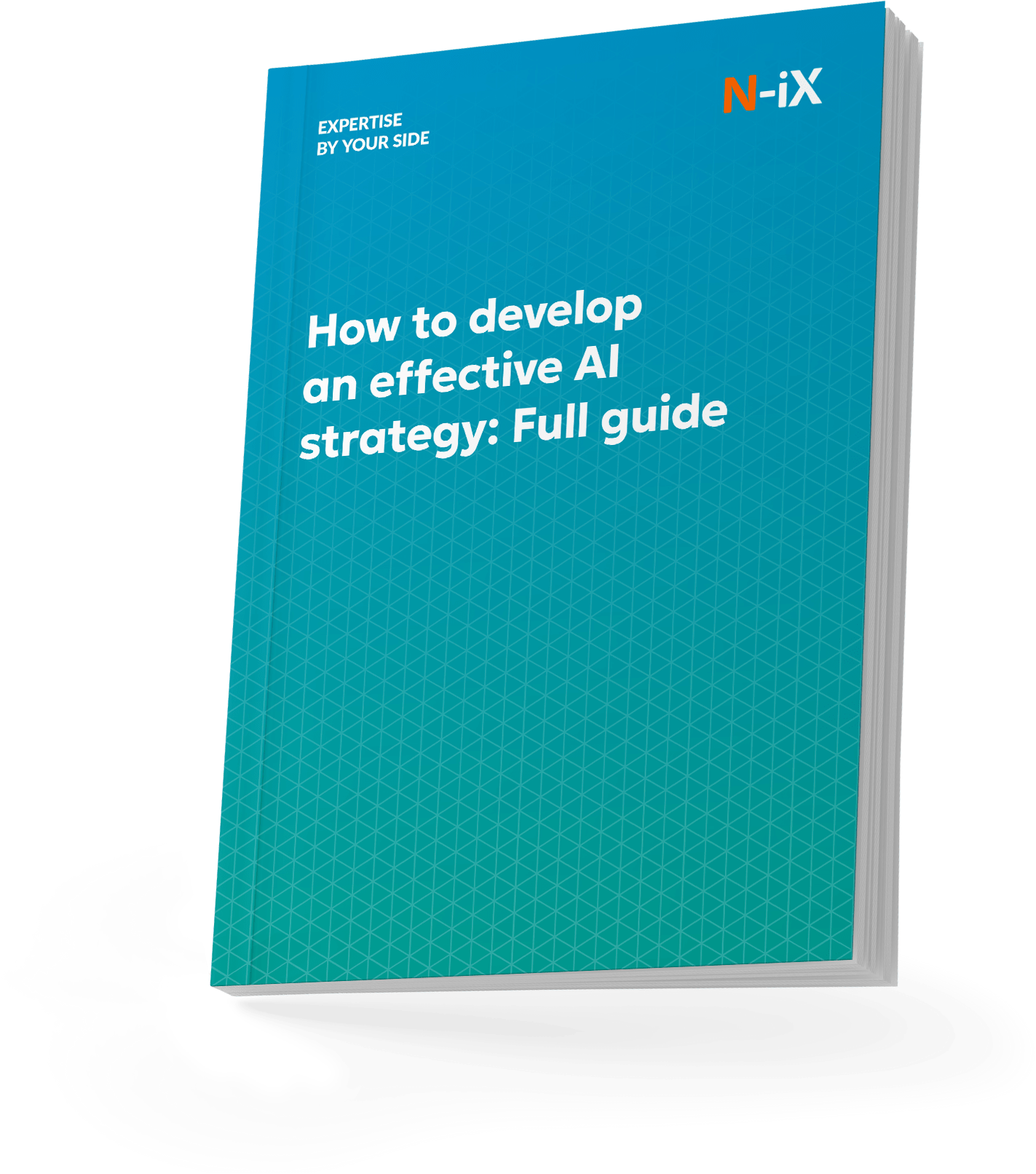
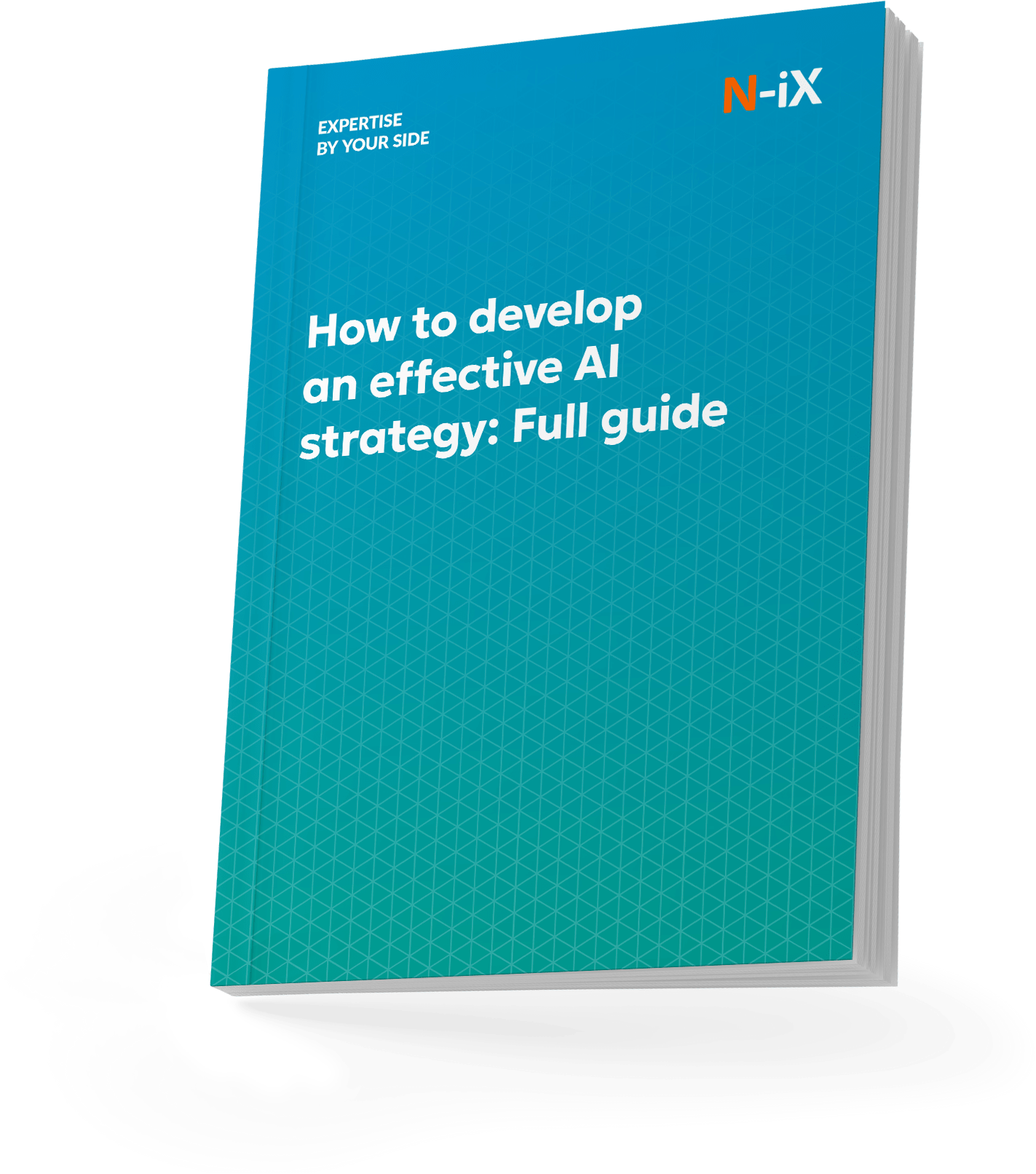
Success!
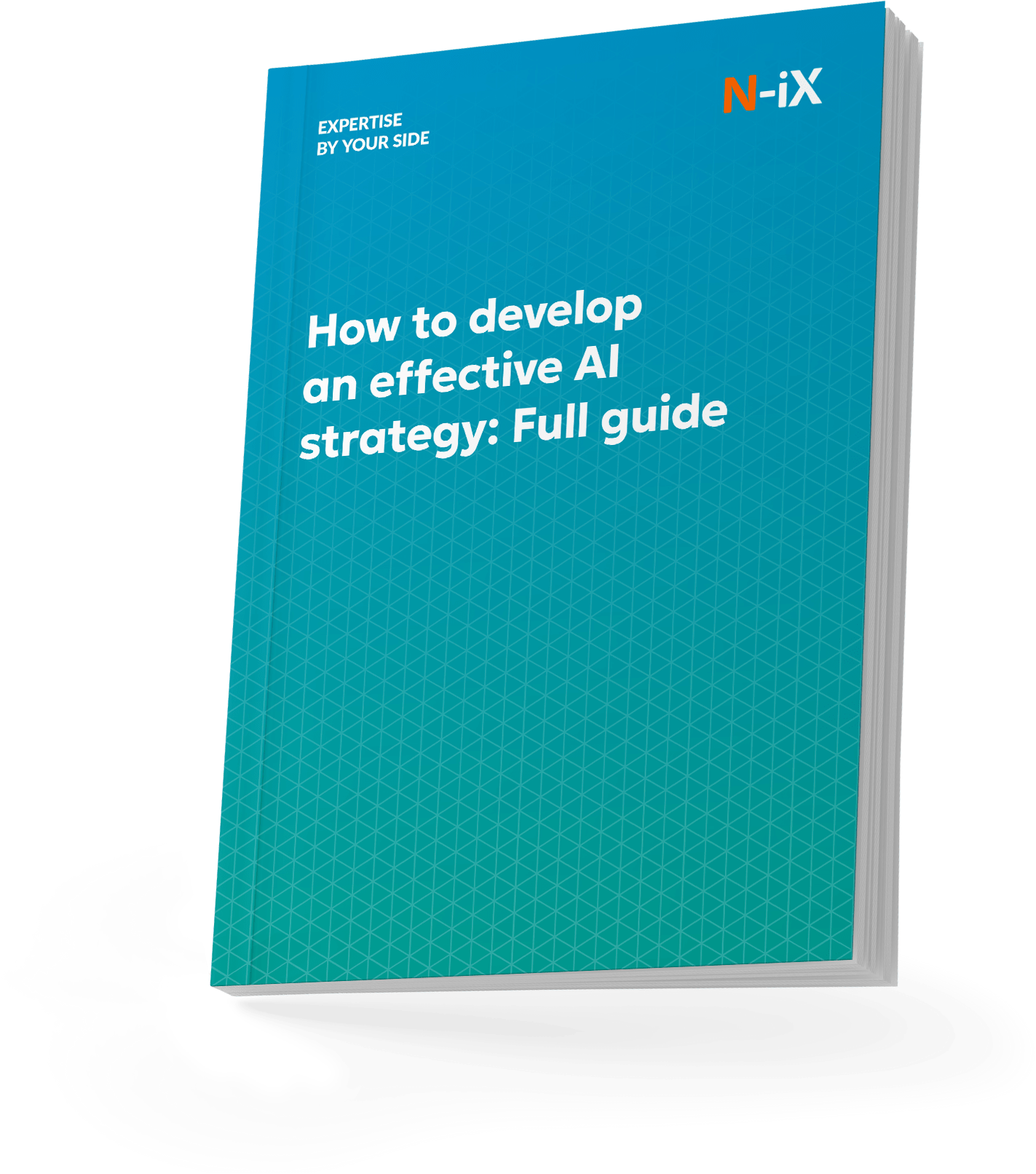
Implementing AI in manufacturing with N-iX: key steps
A structured implementation process is critical for manufacturers seeking to integrate AI into their operations. N-iX helps manufacturing enterprises at every stage, ensuring that AI solutions enhance production efficiency, improve quality, and drive measurable business value. The steps below outline how our experts help manufacturers successfully adopt AI across production, operations, and supply chains.
1. Defining business objectives and assessing feasibility
Our specialists start by aligning AI initiatives to the client’s business goals and identifying critical operational challenges. Common priorities include reducing downtime, improving product quality, automating production lines, or optimizing supply chains.
We assess existing production processes and evaluate available data, such as sensor readings from machinery, quality inspection results, and supply chain information. Our experts check data quality and volume to confirm it meets AI modeling requirements. We conduct a cost-benefit analysis to estimate potential returns and develop a realistic roadmap for AI adoption.
2. Building data infrastructure
Our AI and data engineers consolidate machine data, IoT sensor readings, visual inspection outputs, and ERP system information into unified data pipelines. We eliminate data silos, ensuring that manufacturers can feed AI models with clean and consistent data.
Our team cleans, standardizes, and prepares this data for AI modeling. We design cloud or hybrid architectures capable of processing large-scale data and enabling real-time analytics. Our engineers also implement secure data storage solutions to protect production data and ensure compliance with industry standards.
3. Developing and testing a pilot solution
Our AI specialists develop a pilot solution that addresses a specific operational challenge before scaling the system across production. This could involve building a predictive maintenance model for critical machinery, a computer vision system for defect detection, or an ML-powered tool for demand forecasting.
We integrate the pilot into the client’s production processes while minimizing disruption. Our team tracks performance using key metrics such as downtime reduction, defect detection accuracy, and production throughput. Based on real-world results, we fine-tune the solution to ensure optimal performance under manufacturing conditions.
4. Scaling AI in production and supply chains
Once the pilot demonstrates value, our engineers expand the AI solution across production lines, factories, or supply chain processes. We integrate the system with manufacturing execution systems (MES), quality control platforms, and production monitoring systems.
Our experts ensure that AI-powered automation and data-driven optimization improve production stability, reduce variability, and increase output efficiency. We provide hands-on training to production teams, enabling operators and managers to work effectively with AI systems and interpret model outputs.
5. Monitoring performance and continuous improvement
Our support team ensures that AI systems deliver value as production environments evolve. We monitor performance, retrain models, and adjust system parameters to respond to changes in machinery, product variations, or shifts in demand.
Our specialists conduct regular evaluations to identify potential performance deviations and ensure AI models maintain accuracy. This approach allows manufacturers to sustain operational efficiency, reduce costs, and maintain consistent production quality.
The challenges of AI integration
While AI consulting services can significantly improve manufacturing operations, a successful implementation poses certain challenges. Understanding these intricacies can help mitigate potential pitfalls and ensure a smoother path toward implementing AI in manufacturing processes.
Data quality and availability
Manufacturing thrives on data, yet its quality and compatibility for AI analysis pose significant challenges. This challenge arises from the sheer volume of data combined with inconsistency in formats and siloed sources, creating barriers to seamless AI integration.
The solution is to implement standardized data protocols. At N-iX, we help manufacturers optimize data accessibility for AI analysis through harmonized data formats across systems and the establishment of centralized repositories. Our robust data cleansing techniques enhance data quality and integrity, preparing it for AI-driven insights and actions.
Cost
While AI promises significant improvements in manufacturing, its implementation demands considerable investment. The complexity of AI technologies and the need for specialized skills, data infrastructure, and ongoing maintenance contribute to the perceived high cost of AI implementation.
To navigate the financial aspect, it is important to plan the implementation process and further stages strategically in order to understand cost implications. At N-iX, we collaborate with businesses to develop comprehensive cost-benefit analyses, ensuring a strategic approach to AI adoption. We focus on scalable solutions and phased implementations to effectively manage initial costs while maximizing long-term benefits.
Skill gap
Integrating AI technologies within manufacturing demands a unique skill set that combines AI competence with industry-specific operations. However, a critical challenge is the shortage of interdisciplinary professionals proficient in the nuances of AI and manufacturing processes.
Solving this issue requires finding a reliable software development partner like N-iX. Partnering with us lets you benefit from over two decades of industry experience and a team of more than 200 seasoned middle and senior-level specialists in Data, AI, and ML domains. In such a way, you ensure access to a highly skilled team experienced in orchestrating seamless AI integration tailored for manufacturing.
Compatibility
Integrating AI into existing manufacturing setups or older systems often presents complexities. These challenges emerge due to differing technologies, data formats, or infrastructural differences between AI systems and established manufacturing setups. An instance of such an issue may be when the AI system struggles to communicate effectively with the legacy infrastructure, hindering the smooth data flow or process integration.
To avoid these issues, we conduct comprehensive compatibility assessments. For this purpose, our team meticulously evaluates your current manufacturing systems and infrastructure to identify potential points of conflict or misalignment with the proposed AI solution. Our experts work closely with your company throughout the whole process of AI implementation, starting from the initial assessment phase. This collaborative approach ensures a clear understanding of your infrastructure and operations. Due to planning and transparent communication, we create an AI implementation strategy that mitigates potential disruptions and ensures optimal performance within your manufacturing operations.
Security
Securing data and adhering to industry regulations during data collection, storage, and utilization in AI-driven processes involves working with sensitive information. Manufacturing data often encompasses critical details about processes, product designs, and even proprietary information. To ensure its security, it is necessary to manage a vast volume of data and safeguard it against potential breaches, unauthorized access, or cyber threats at the same time.
To address these challenges, we fortify data security with stringent measures aligned with industry standards and regulations. This includes implementing encryption protocols and access controls to shield sensitive data in your Artificial Intelligence manufacturing applications.
You may also be interested in: How to choose a competent artificial intelligence solution provider
Wrap-up
AI is at the heart of modern manufacturing, expanding its influence annually and helping companies increase their performance and stay competitive. As AI continues to shape manufacturing, integrating it isn't just an option; it is necessary for future success.
Partnering with an AI development company is key to fully leveraging the potential of AI in the manufacturing industry. As your software development partner, N-iX can help you find the optimal solution to fortify your company’s efficiency, enabling efficient investment for maximum returns.
Have a question?
Speak to an expert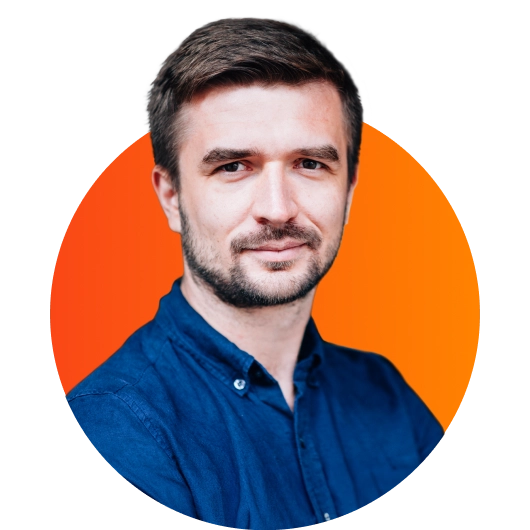